Paving slabs have long ceased to be exotic. The material has long and firmly settled on the streets of cities and paths of private houses. After all, not one person will refuse to transform the adjoining or garden space. Tiles can be purchased, but more economical option- do it yourself.
How to prepare high-quality paving slabs that will last for decades?
In general, release paving slabs- a very profitable business niche, the development costs of which will not become too exorbitant. And today we will consider the proportions of the composition for production of paving slabs
We prepare a solution for paving slabs at home
Here you will need:
- sand;
- pure water.
In the process of home production, there is no special need for strict adherence to GOST standards. And the mix is pretty easy to make. Here are some recipes.
You need to take sand and cement in a ratio of 1.5 to 1. Mix the components thoroughly and only then add water little by little. The result should be a mixture with the consistency of good dense sour cream.
If you are not too friendly with proportions, then use ready-made numbers:
- sand - 7 ten-liter buckets;
- cement - 2 buckets of brand M 400 (you can also take M 500);
- clean water - 15 liters.
Please note that after the end of the kneading, the finished solution should not stick to either the shovel or the walls of the container.
There is a more perfect mixture for "home" paving slabs. In this case, C-3 plasticizer is additionally mixed with the usual ingredients. This is a special additive that provides frost resistance of the material. The proportional ratio looks like this:
- cement - 550 kg;
- sand - 1650 kg;
- plasticizer - 5.5 kg.
To check the readiness of the mixture, roll a bun out of it. It should not stick to the palms.
You can also make colored tiles. In this case, it is better to mix the two types of solution. One regular and one with color. To make a colored solution, you will need to add crushed stone or microsilica in the amount of 55 kilograms to the original recipe.
Industrial production of paving slabs
If you decide to seriously engage in the production of paving slabs, then you simply must adhere to GOST standards. You must take into account all the requirements so that the finished material meets accepted standards. Also, in the future, you must adhere to the choice made earlier so that the products do not differ in quality. This is especially true of the brand of cement and the color of the color scheme.
For the preparation of concrete, it is best to use cement M 500. Grade M 400 has a higher consumption. Crushed stone and sand are used as aggregates. It is best to use crushed granite. But if it is not possible to buy just such, then it can be replaced with fine-grained concrete.
Higher quality cement M 500
Mixtures for the manufacture of paving slabs are not complete without special additives. The most commonly used dispersant or plasticizer. Rarely others. The main purpose of the mineral additive is to improve the quality characteristics of the material, in particular water resistance and durability. Such additional mineral components also provide frost resistance of the tile. The percentage of the additive to the weight of the cement used should be 0.15%.
And now about dyes. It is better to use inorganic dyes from foreign manufacturers. They have good performance. Therefore, 2-5 percent of the mass of cement added to the total mixture is quite enough for the tile to get a good saturated color. Russian paints must be added at a rate of 8%.
The prescription proportions that have been given will help establish the manufacturing process of really high-quality material. This will certainly affect the development of the business, since quality is always appreciated. Good luck!
Comments:
To make paving slabs at home, you will need a properly prepared mortar for paving slabs and a minimum of necessary equipment. To prepare a high-quality solution, an ordinary concrete mixer is enough, but to make paving slabs at home, you will have to come up with a replacement for a special vibrating table with limiters and purchase or make your own molds for pouring.
For the manufacture of paving slabs on your own, you need a correctly prepared mortar for paving slabs and the necessary equipment.
Methods and technology for the manufacture of paving slabs
In industrial conditions, paving slabs are produced in two ways - vibropressing and vibrocasting. To organize the vibrocompression of dense concrete mixtures, a special expensive press is required, so the use of this method in domestic conditions is not yet discussed.
Vibrocasting technology is cheaper and easier to use, and therefore more common. This technology is used not only for the manufacture of paving slabs, other concrete products are also produced by this method: poles, road curbs, foundation blocks and even concrete slabs of panel houses.
The main working tools of the process of vibrocasting paving slabs are a vibrating table and a concrete mixer. The vibrating table is a rigid steel structure with a vibrating working surface and is designed to compact loose materials and remove air bubbles from them. A concrete mixer is used to mix the dry components of the mortar, therefore, in production conditions, special devices are used with blades located inside the drum.
To prepare the solution, the following materials are needed:
- granite screenings;
- cement M500;
- river sand;
- special plasticizers;
- water.
However, when making tiles at home, it is expensive to purchase a vibrating table, so a home-made vibrating table is used instead, made from a rectangular steel plate welded to a corner. Then chocks or bricks are placed under the corner - a working surface is obtained that can transmit mechanical vibrations. It is enough to lightly tap on the molds with the poured solution placed on such a surface, and the steel plate vibrating from tapping will transmit vibrations to the solution in the molds located on it, compacting it.
Back to index
Recipe for mortar for paving slabs
The recipe for a mortar for paving slabs is quite simple to execute, but to obtain a high-quality final product, you need to use only high-quality ingredients, and also strictly observe all proportions of the mortar.
In the manufacture of paving slabs at home, it will not be possible to strictly adhere to the requirements of GOST for this type of product, therefore, it is permissible to replace some components of the solution. So, if it is impossible to purchase granite screenings, it can be replaced with home-made fine-grained concrete without compromising the final quality.
Instead of river sand, you can also use ordinary, but always sifted, in order to rid it of clods of earth and impurities to the maximum. If the manufactured paving slabs are planned to be used for garden paths, where tractors and cars will definitely not drive along it, then the cheaper M400 brand can be used instead of M500 cement.
If a concrete mixer is not available, then at home it can be replaced with a construction mixer or an electric drill with a rotating nozzle. If none of the listed tools is available, and the amount of work is small, then you can prepare a sufficiently high-quality mixture manually, using an ordinary shovel.
The composition of the mortar to obtain 1 m² of tiles gray color 45 mm thick includes:
- cement (20 kg);
- sand (22 kg);
- granite screenings (44 kg);
- plasticizer (75 g);
- water (15-17 l).
If you want to make a colored tile, you need to add a dye of the appropriate color to the mixture. For the indicated volumes, the consumption of coloring pigment will be at least 700 g, and if you want to get a more saturated color, its consumption must be increased. Also, in addition to the plasticizer, it is possible (but not necessary) to add a special dispersant to the composition of the mortar for paving slabs to increase frost resistance. For the indicated volumes, 90 g will be needed.
Back to index
Solution preparation sequence
The preparation of the solution should always begin with the preparation of the plasticizer and dispersant. They are prepared in advance, because. their main purpose is to significantly speed up the process of setting the solution. Water for the preparation of these components should be slightly above room temperature - about 40º. To dilute 75 g of plasticizer, 5 liters of water will be needed.
First, prepare the dry mix. To do this, mix sand with granotsev in a ratio of 1: 2 until a homogeneous mass is obtained. When preparing a colored tile, the coloring pigment is mixed with these components at the same time. When mixing in a concrete mixer, the process takes 20-25 seconds. When using other mixing tools, the cooking time will have to be determined by the uniformity of the composition of the dry mix.
Having achieved the desired result, cement is added to the prepared mixture and again everything is thoroughly mixed. On the final stage water is added to the mixture, and at the very end - a diluted plasticizer. When adding water to the composition, it must be borne in mind that at the end, along with the plasticizer, a certain amount of water will be added to the mixture. If you lose sight of this, then the mixture will turn out to be too liquid, and you will have to correct the situation by gradually adding sand and cement. When the solution is prepared in a concrete mixer, this will not create any particular problems, but when preparing it with a shovel, it will take a lot of time, effort and nerves, especially considering the fact that due to the added plasticizer the solution will set much faster, so you will have to mix not only thoroughly, but and as quickly as possible. A properly prepared mixture should stand on a trowel with a slide. But, poured into the mold, with the slightest tapping on it, the mixture should blur, filling the entire space.
Back to index
Formation of mortar tiles
As soon as the solution is ready, it must immediately be poured into molds.
Delay in pouring is unacceptable, since the plasticizer added to the solution significantly accelerates setting.
The resulting solution must be poured into the mold first with a thin layer of 1 cm, and then pour the main layer on top.
Before pouring the mixture into molds, they still need to be prepared. Forms need to be lubricated with a special compound that can be purchased at a hardware store. If you decide to save on this composition, then you can lubricate them with ordinary sunflower oil, although such a process will look quite peculiar.
Each form must first be thoroughly lubricated with a paint brush and immediately after lubrication also thoroughly blotted with a rag. The surface of a properly prepared form should be slightly greasy, but there should be no visible drops of oil on its surface. Only in this case the surface of the tile will be even and smooth, without tubercles and air bubbles.
Lubricated forms are placed on a steel plate, filled with the prepared solution and compacted within 2-3 minutes. To do this, you need to tap on the plate with something heavy enough, preferably with a wooden or rubber mallet.
In the first 30-40 seconds, you need to tap quite intensively, then the intensity decreases so as not to overdo it and break the forms. You need to tap not in one place, but over the entire area of \u200b\u200bthe impromptu vibrating table, so that all the exposed forms are subjected to vibrations of the same strength and frequency.
After shaking, the surface of the solution in the molds must be smoothed with a trowel. Then cover the forms with plastic wrap, if the forms are in the sun, then you need to additionally cover them from the sun and leave for 2-3 days. And only after this period, the formed tiles can be knocked out of the molds.
Before knocking the tiles out of the molds, since they have not yet acquired the desired strength, it is better to lay a wadded blanket, straw, etc. because when hitting solid ground they may crack. Before knocking out the tiles, the mold with the frozen mortar should be lowered into warm water (about 50 ° C), and then, lightly tapping the walls of the mold with a mallet, wait until the finished tile falls out of the mold. The formed tile must be kept in a cool, darkened room for at least 1.5-2 weeks, and only after that it will be ready for use.
Knowing the exact proportions of the solution and the subtleties of its preparation, everyone, having shown a minimum of ingenuity and ingenuity, will be able to prepare at home the amount of high-quality paving slabs necessary for their own needs.
Thanks for the feedback
trend to decorate land plot or city streets with paving slabs has long gained popularity. Today there are many varieties of this product for landscape design for every taste. Tile manufacturing technologies have developed and simplified so much that the process can easily be done with your own hands at home. Let's find out what is the composition of concrete for paving slabs, how is this decorative coating made?
Paving slabs made from concrete mortar have a lot of advantages over other street coverings. The main advantage here is the simple manufacturing process. Due to the composition, the finished product is very strong, resistant to any mechanical influences. This feature in a positive sense distinguishes concrete paving slabs among various materials of a similar purpose.
Sidewalk coverings, which are based on concrete, are not afraid of precipitation, wet weather, because they have an increased. The material perfectly tolerates temperature extremes, is able to withstand any frost, which makes it possible to use it even in the North. In addition to these positive features, there are others in concrete paving slabs. good qualities:
- strength;
- durability;
- variety of products in terms of shape and color scheme, allowing the customer to choose exactly the option that he needs;
- simplicity, which does not require special skills, abilities, which is easy to implement with your own hands;
- aesthetics and attractiveness of the product;
- easy maintenance and repair, not taking much effort.
Components for tile mortar
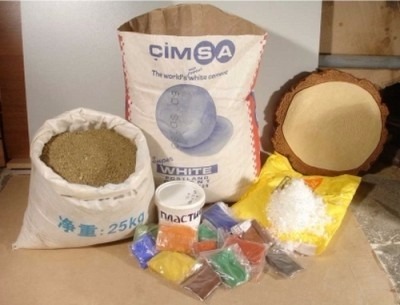
These ingredients include:
- concrete;
- sand from quartz or other crushed rocks;
- gravel;
- water;
- pigment (added at the request of the manufacturer).
For the manufacture of concrete, exceptionally heavy grades of cement marked M300, M350, M400, M450 are suitable here. For sand concrete, cement grade M400 is used. A large filler can be stone or gravel with a minimum diameter of 1 cm. For better solidification of the product, heated water should be used.
It also does not do without additional impurities. For example, polypropylene threads that increase the wear life of tiles; or additives that make the product resistant to moisture and temperature fluctuations. Separately, I would like to focus on pigment substances that give the product a different color and aesthetically attractive appearance.
You can check the quality of the released product by knocking two tiles against each other. If the recipe was used correctly during the preparation of the mixture, and the proportions were exactly maintained, the sound during the blow will come out sonorous. If there is a dull sound, it means that during production process It was a mistake.
Because of this, the quality of the material suffers, problems may arise during its operation. Most often, such consequences arise due to the use of poor-quality clay sand or too much poured liquid.
Manufacturing technologies
To date, there are two types of production of landscape coatings from concrete composition.
vibrocasting
The essence of the method is to compact the prepared mixture inside special plastic molds by means of intense vibration. Vibratory movements are carried out with the help of an electric motor, to the shaft of which an eccentric is attached. A container with concrete inside is placed on an oscillating platform, kept there for some time.
Then, after shaking, the molds with the mixture are transferred to heat for two days. The finished product is removed from the mold inside the thermal pool filled with water heated to 70-80 degrees. It is highly undesirable to carry out the removal of the product before the deadline, since unseasoned tiles tend to crack and chip.
With this production method for the manufacture of concrete, proportions of 1: 2 are used - 1 part of M500 cement, 2 parts of aggregate. The ratio of coarse and fine aggregates should be equal. Dry raw materials are laid inside the concrete mixer, only then water is poured there.
If you want to make the product colored, add the desired dye, but not more than 5% of the total mass of the composition. Polypropylene fiber, which also performs a reinforcing function, will give the composite a higher flexibility.
It is possible to improve the quality, as well as performance, by adding to. Paving slabs created using the vibrocasting method stand out among other similar products due to their smooth glossy surface and aesthetically pleasing appearance, as well as a large assortment for every taste, while delighting customers with affordable prices.
A large amount of water used has a worse effect on resistance to sub-zero temperatures. This problem is eliminated by adding modifying agents. However, the final cost of the product will increase significantly from this. Vibrocasting tiles come out of different thicknesses, which can make laying somewhat difficult.
Vibrocompression
The technology is based on the use of a special matrix with a composite placed inside, which is fixed to a permanently oscillating vibrating table. over the mixture with great strength a punch is hoisted (a part of a vibropress moving inside it, like a piston). When the matrix is removed, the finished formed product remains on the platform. The advantages of this method are increased productivity, plus full automation of the process without the cost of human labor.
Vibropressed tiles are made in a ratio of 1: 3 - for one share of M500 cement, three shares of sand or other fine aggregate are used. Here you should not use a lot of liquid, as this can reduce the strength characteristics of the product being created.
It is possible to improve the performance properties of the future product by adding plasticizing, plus fiber materials. How much to mix the dye depends on how saturated the manufacturer wants to make the color of the future flooring.
Products made using this method have a clear geometric shape, a rough, non-slip surface, thereby making it easier for people to move along the tiled paths during icy conditions. Sidewalk coatings obtained by vibrocompression perfectly store the brightness of their shade throughout the entire service life, which is approximately 25 years.
Unfortunately, the same cannot be said about vibrocasting products. Vibropressed tiles are easy to grind, polish, bush hammer. Defective products are much less common than in vibrocasting production.
Used materials, tools
To create a do-it-yourself sidewalk covering using the vibrocasting method, you will need the following materials:
- aggregate;
- cement sand;
- plasticizer;
- dye;
- reinforcing fiber;
- water.
For work you will need:
- concrete mixer;
- vibrating device with a flat surface;
- molds (it is better to buy ready-made ones);
- large container filled with warm water.
In addition, you should have with you:
- strong 10-liter bucket;
- Master OK;
- rubber gloves.
Manufacturing process at home
Thanks to the simplicity of the technology, pouring paving slabs on your own will not be difficult. At the same time, if you do everything right, according to the recipe, the quality will come out no worse than that of factory products. rinse well before use. If you use a pigment, then take the one in which you are sure that it will not let you down.
If a volume of about 130 liters is used when creating a solution, then gravel filler can be taken. Pour in as much liquid as the solution needs to gain the desired density. Then you can mix in the plasticizer.
We present to your attention an approximate recipe for the solution. For 30 kg of M400 cement, 17 liters of liquid will be needed. First, 1.5 buckets of sand are poured into the concrete mixer, 7 liters of water are poured in, and it is stirred for half a minute. Then all the cement is added, 8 liters of water, mixed again, forming a cement paste. After this mass begins to lag well behind the walls of the mixer, the remaining sand and water are mixed there. Then everything needs to be stirred for a few more minutes.
For the preparation of a two-layer pavement, the proportions are slightly different. The initial layer is made of sand and cement in an equal ratio. These components are mixed until a consistency similar to sour cream is formed. Next, the resulting mixture is transferred inside pre-prepared forms.
The next step is to prepare the second ball. Here are used: 1 portion of cement, 3 portions of sand filler, 2 portions of gravel. When the composite stops spreading, then it will be ready. The prepared solution is transferred inside the molds on top of the first ball.
Summing up
As you can see, creating a tiled material for paving is not particularly difficult. It is quite possible to do it yourself at home.
If you follow all the rules of the production process, the ratio of components according to the recipe, then you will get an excellent, high-quality product that will not only decorate the landscape near your home, but will also serve faithfully for more than one decade.
Nowadays, it has become popular to use paving slabs. It has many advantages over other pedestrian street surfaces, and its composition provides resistance to weathering, repeated winter-summer cycles. Paving slabs can cover both entire areas and your own paths. GOST contains requirements for various types tiles, which must be carried out during production to ensure its durability.
The recipe for the preparation of concrete should be strictly observed, the requirements for the ratios of the components - for the sake of the quality of the final product.
The composition of the mortar for tiles
Necessary qualities for the tile composition:
- Abrasion resistance, wear resistance.
- Finely porous structure.
- Small water absorption.
- Frost resistance.
More about the components:
- Cement. For the preparation of concrete, cement is needed; for paving slabs, Portland cement grade 500 and higher is used. Lower quality cements will not be able to provide the required quality.
- Sand. Acts as a small filler. Applies middle group sand, modulus of fineness is about 2 (according to GOST 8736-93), you need to use raw materials from river quarries. The sand must be sifted, free of excess impurities and debris.
- Rubble. Granite chips are used as a coarse filler, which improves the strength of the tile and its frost resistance. Fractions ranging in size from 5 to 10 mm, and needle and lamellar additions are less than a quarter of the volume of granular crushed stone. This material should only be used in the washed state. Suitable crushed stone from igneous rocks, for example, granite, GOST 8267-82. The compressive strength grade is required from 1000 and above, and the frost resistance is above 200.
- Additives and plasticizers - give plasticity to the raw mass of concrete, prevent delamination and cracking both during drying and use, add water-repellent properties to the concrete mix, the product becomes less brittle. When using plasticizers, they should first be diluted in warm water, which will be added to the concrete solution. In this case, the addition occurs with constant stirring of water and the gradual addition of a plasticizer. Plasticizers are added in proportions from 0.5 to 1% by weight of cement.
To achieve high strength characteristics, alkali-resistant polypropylene, polyamide and glass fibers can be added to the concrete composition, in a mass of about one kilogram per cubic meter of solution.
- Coloring substances. The multiplicity of the color palette of tiles is carried out by adding dyes and pigments to the concrete mixture. Requirements for dyes - high resistance to ultraviolet and alkalis, since the paving surface will have to experience large solar loads, and cement has alkaline properties. Pigments, like plasticizers, are mixed first in water, and then the mixture is added to the cement. You need to add in a proportion of 3 to 15 percent by volume of cement, depending on the desired color saturation. It is not recommended to add too little or, conversely, a lot of dye, since a small amount gives a bad color, and a large amount lowers the strength characteristics of concrete and increases the demands of the solution on water. The proportions are indicated in the instructions for the pigment from the manufacturer.
- Water. Here it is worth strictly following the recipe, since an excess amount of water will lead to an increase in the drying time of the finished tile and a decrease in its quality. Water should be taken purified from dirt and impurities.
Component ratio
It is recommended that in the manufacture of paving slabs, strictly follow the GOST standards and manufacturing rules, their non-compliance will lead to a deterioration in product quality. If necessary, you can add a little water to the composition. The main thing is that the finished solution is well mixed.
The composition of mixtures for the production of paving slabs - a table of proportions
Cement, sand and crushed stone are mixed in a ratio of 1/2/2 to obtain normal quality concrete. Below is the recipe concrete mix based on a bag of cement weighing 50 kg. General proportions, recipe and composition can be found in GOSTs and SNiPs, and clear technical requirements are spelled out in GOST 17608-91.
- Water 15–20 liters (2 buckets), the exact amount depends on the moisture content of the bulk materials used.
- The plasticizers included in the composition, according to the requirements, are diluted in a small amount of warm water and then poured into a concrete mixer to the rest of the water, mix.
- Add the dye for paving slabs, stir.
- Three 12 liter buckets of clean gravel fall asleep and wait for everything to mix.
- Pour into the resulting mass the cement included in the composition, divided into 3-4 portions, giving time to mix each portion.
- We fall asleep another bucket of rubble and after mixing we fall asleep 4 buckets of sand, just like cement, mixing each bucket.
- Add the last bucket of gravel, mix everything thoroughly.
This is followed by casting and laying out raw paving slabs for pre-drying. After a few hours or a couple of days, depending on the atmospheric drying conditions and the proportions and the recipe, you can remove the molds, and then continue drying the finished product for two weeks.
Properly selected composition of the solution for paving slabs allows you to implement one of the most beautiful and practical ways to improve paths and playgrounds on your site - paving with paving slabs.
Paving slabs will help create various patterns on the territory of the house.
The use of such material is not in vain widely used throughout the world. The coating is durable, creates a special attractive appearance and is an important element of landscape design. Currently, you can find styling elements for every taste from different manufacturers. However, high-quality tiles can be made with your own hands. To do this, you need to choose the optimal composition of the solution for paving slabs and follow all the recommendations for manufacturing.
Features of paving slabs
Paving slabs are plates of various shapes and sizes to cover pedestrian and traffic areas on a personal plot. Tiles can be made from a variety of materials, but the most common are concrete elements that are preformed and ready to use.
Among the most popular forms of such elements, the following can be distinguished: brick (rectangle), square, "paving stones" (rectangle with side profiles), "wave", hexagon ("honeycomb"), Z-shaped view, etc. The shape of the tile can be the most bizarre, depending on its purpose and the wishes of the owner. Using paving slabs, you can create various patterns on the site.
The color of the coating can be natural, but quite often a multi-colored material is used, which is obtained by introducing a dye. Tiles can vary in size. For the quick formation of paths, large squares with a side of 30 - 60 cm and a thickness of 6 - 8 cm are used. For decorative coating, profiled tiles from 10 to 30 cm in size and 3 - 8 cm thick are used.
Material selection
Paving slabs are designed for outdoor use under the influence of mechanical loads. With this in mind, the following requirements are imposed on it: high compressive and bending strength, wear resistance, frost resistance, water resistance and resistance to various substances (oils, alkalis, salts), direct sunlight and temperature extremes. In addition, tiles should not be slippery even when wet. At the same time, it should have a minimum cost and good appearance.
The concrete mixture with the addition of plasticizers and other special agents fully meets all the requirements. The solution for paving slabs is made on the basis of cement, sand and gravel with the addition of a plasticizer, modifier, reinforcing components, coloring pigments and the right amount water. Given the increased strength requirements, it is best to use Portland cement M500; it is recommended to use pure Portland cement brand PC I-500, designed for a load of at least 500 kg / cm².
The filler is sand. It is desirable to use river sand, purified from impurities, with a coarse-grained fraction (at least 2 mm) with a clay content of no more than 3%. As a filler, crushed stone of an average fraction (5-10 mm) is used, which has increased strength and frost resistance. For paving elements, high-strength and wear-resistant crushed granite is most suitable.
Plasticizers and modifiers are necessarily introduced into the composition of the concrete solution, providing high quality material and crack-preventing tiles. It is recommended to use standard additives: S-3 plasticizer and PFM-NLK modifier. Strengthening of the elements is achieved by introducing a reinforcing element in the form of a polypropylene fiber into the structure of the mixture. You can use polyamide or glass fibers with a length of about 10 - 20 mm, with a diameter of up to 40 microns. Dyes should not impair the properties of concrete. They must be resistant to washout, solar radiation and various temperatures. The most suitable are pigments based on iron oxide.
Choice of manufacturing method
The manufacture of paving slabs is carried out in molds using vibration, which ensures a uniform dense structure of the elements. Basically, 2 manufacturing methods are used: vibropressing and vibrocasting. Vibrocompression means less water and a denser structure. With this method of forming the product, it is possible to reduce the amount of plasticizer. But it will require the application of pressure on top of the mold during the vibration process.
Vibrocasting is carried out in two stages with the obligatory introduction of a plasticizer and with a large amount of water. First, the first layer with a thickness of about 2 cm is poured, and after its shrinkage, when the vibrator is turned on for a short time, a second layer of the desired thickness is formed. At home, a simplified method is sometimes used, when the vibrating table is replaced by simple manual shaking. The quality of such tiles will be somewhat worse than the quality of the elements obtained by vibration, but quite satisfies the requirements for not too much abrasion of the tiles after laying.
Solution composition
When preparing a mortar for paving slabs by vibrocompression, a cement-sand composition is used. The following recipe for 1 m³ of concrete is recommended: cement M500 - 700 kg, river sand - 1350 kg, water - 160-170 l. The solution is thoroughly mixed and poured into molds, where vibration under pressure is provided.
In the case of vibrocasting technology, 2 layers of different composition are formed. The top (textured) layer has the following formula for 1 m³ of mortar: cement M500 - 600 kg, river sand - 1550 kg, plasticizer and modifier - 6 kg, polypropylene fiber - 0.8 kg, pigment - 18 kg, water 180-200 l . The lower (main layer) is recommended to be made in the following proportion: cement M500 - 600 kg, river sand - 850 kg, crushed granite - 750 kg, plasticizer - 3 kg, water 170-180 l.
Tools for the job
When making paving slabs from concrete mortar with your own hands, you will need the following equipment and tools:
- vibrating table;
- vibrator;
- shovel;
- concrete mixer or construction mixer;
- measuring bucket;
- pallet type container;
- putty knife;
- Master OK;
- ruler;
- scales;
- a hammer;
- mallet;
- paint brush.
Preparation of ingredients
Mixing of concrete is carried out after preliminary preparation of the ingredients:
- The plasticizer is mixed with water in a ratio of 1:3 at a water temperature of about 35 - 40 degrees in 2 stages: mixing for 10 minutes, a daily break, so that the mixture is infused, repeated mixing for 15-20 minutes. After that, the plasticizer is introduced into the concrete mixture.
- Dye: the pigment is diluted with warm water to the consistency of thick sour cream, settled for at least 1 hour, after which it is introduced into the solution.
The concrete solution is prepared in the following order: sand with dye is poured and mixed, crushed stone is loaded, then cement is poured, water is poured, a plasticizer and polypropylene fiber are added. Everything is thoroughly mixed until a thick concrete solution is obtained.
Simplified technology solution
A simplified do-it-yourself technology for making paving slabs is widely used: the form is poured with concrete mortar completely to the desired thickness and periodically shaken by hand to compact the mass.
The solution for this method is made of cement, sand and gravel in a ratio of 1: 2: 2 in the following order:
- Clean water is poured in about 20 liters (2 measuring buckets).
- The plasticizer and dye are diluted.
- Crushed stone (3 buckets) is poured, and then gradually, thoroughly mixing, cement (50 kg).
- Crushed stone (1 bucket) and sand (4 buckets) are poured while mixing the solution.
- Crushed stone is added (1 bucket).
- Fiber is added.
Everything is thoroughly mixed until a homogeneous thick mass is obtained.