Comments:
- Proportions of concrete per cube
- Grade of concrete for overlapping
The choice and purchase of a particular brand of concrete depends on the purpose of this material. The table of concrete proportions shows what ratio of components is present in a particular brand of concrete. Usually, the project documentation clearly indicates which brand of concrete should be used in the construction of the facility. The numbers and designations M100, M200, etc. indicate the ultimate compressive strength of the material.
To prepare high quality concrete mix it is necessary to observe all proportions correctly.
The strength of concrete tends to increase throughout the entire hardening cycle. After 2-3 days after pouring the mixture, one strength indicator is determined, after 6-7 days - another. Under suitable weather conditions, after a month, concrete is gaining design (calculated) strength. The range of concrete grades starts from grade M50 and ends with grade M1000. In the construction of residential buildings, the range from M100 to M500 is usually used. If the concrete mixture will be made independently, it is necessary to strictly observe all the recommended proportions of the constituent components.
Preparing concrete by hand
For those who have never dealt with construction, it is often difficult to understand what a concrete mixture is and how to make it right. But even having great experience construction of various objects, you may not know some of the nuances.
It is not at all difficult to make concrete for the construction of a foundation or garden paths on your own. Mixing should be done in an old trough or bath. If a small volume of solution is required, then you can use an old box, which you do not mind throwing away later. If a large volume of mortar is required, it is necessary to use special tools in the manufacture: a drill with a special nozzle, a concrete mixer. For kneading, you can also use an ordinary shovel, small garden pitchfork, hoe, or any other suitable device. However, before proceeding with the manufacture, you need to carefully select the appropriate components: sand, gravel, cement and water.
The strength of concrete primarily depends on the quality of the cement. Therefore, his choice must be approached with special care. When buying material, you should pay attention not so much to the manufacturer, but to appearance material and storage conditions. It is imperative to pay attention to the date of manufacture of cement. Over time, its activity is greatly reduced. High-grade cement loses its positive characteristics especially quickly. Fresh material when squeezed in the palm of your hand will not turn into a lump and will easily pass through your fingers.
Some unscrupulous suppliers even provide fake material - cement mixed with dolomite dust, mineral powder, ash and other fillers. When using it, the concrete begins to set more slowly, and after hardening it acquires insufficient strength. When using low-quality material, a month after pouring into concrete, it will be very difficult to hammer a nail.
When making a concrete mix, it is equally important to choose the purest possible sand, which will not contain impurities in the form of silt, limestone or clay. Crushed stone should have a rounded shape, its grains should not be more than 50 mm. Most optimal size- 5-20 mm. When preparing a concrete mixture for a screed, for example, a special mixture is made with expanded clay with a fraction of 5-10 mm.
Back to index
The ratio of components in the concrete mix
The table of compositions and is indicated in GOST 7473-94 and in SNiP 5.01.23-83. In order to correctly observe all these proportions, it is necessary to take into account the density of all the ingredients included in the composition and the construction conditions. Pouring and preparing a concrete solution is possible only after a full calculation of the entire required volume and weight of the components of the concrete mixture. In the presented table, you can see what composition and proportions of the components should be in M400 grade concrete.
The table shows that the largest proportion is 1 part of cement, 3 parts of sand and 6 parts of crushed stone. In addition to these components, 0.5-1 parts of water should be added to the mixture in order to obtain the required consistency of the solution. You should not immediately pour out all the prescribed part of the water: this can lead to an undesirable result that will be very difficult to fix.
The calculation of proportions is done according to regulatory documents. However, it should be borne in mind that not all table parameters can be thoroughly used in practice when preparing a batch. For example, sand can have different moisture content, which significantly affects its weight and volume.
In order to optimally approximate the normative indicators to the real ones, it is necessary to dry the sand and gravel as best as possible.
A convenient container can be filled in turn with various components (without tamping) and determine the weight of the desired proportion. After that, the required proportion of each component in the bucket ratio is determined.
Back to index
Proportions of concrete per cube
To obtain the correct consistency of the concrete mixture, the following indicators must be considered:
Crushed stone for the preparation of concrete should have a rounded shape, and its grains should not be more than 5 cm in diameter.
- the required strength of the material;
- proportions of components;
- required plasticity;
- brand of cement;
- characteristics and properties of components.
For example, to get the 1st cube of M200 concrete, you need to take the following amount of materials:
- Cement - 330 kg (0.25 m³) with a bulk density of 1300 kg / m³.
- Crushed stone - 1250 kg (0.9 m³).
- Sand - 600 kg (0.43 m³).
- Water - 180 l (0.18 m³).
When summing the volumes of each component, 1.76 m³ is obtained. Although in fact it turns out 1 cube. All the ingredients, mixing with each other and filling all the voids, form a dense mixture without air bubbles.
- Brands and proportions of concrete
- The sequence and proportions of adding components in the preparation of the concrete composition
When building a house or other structure, it is often necessary to prepare concrete on site. - the process is simple, but requires certain knowledge. First of all, it should be borne in mind that there are various.
Its composition, the proportions of the constituent components differ depending on the purpose of use.
The greatest requirements are put forward for concrete used in the construction of nuclear power plants, bridges and other strategically important facilities.
Brands and proportions of concrete
Concrete should be selected according to the brand, which determines the degree of its strength. The brand itself shows the maximum load per 1 cm² of area. The load is measured in kg (for example, concrete grade 200 can withstand a mass of 200 kg over an area of 1 cm²). Thus, you can easily choose the right brand of concrete.
To prepare concrete grade 100, cement grade 400, crushed stone and sand are mixed in a ratio of 1:6:3. This concrete is widely used when pouring the first reinforced belt - grillage. For the preparation of brand 200 concrete, the following proportions of the components are used: 1 part of brand 400 cement, 2 parts of sand and 5 parts of crushed stone. This will have greater strength and can be used in the construction of floors, load-bearing structures, reinforced belts and other elements that take significant loads. The proportions of concrete preparations from cement grade 500 can be seen in Fig. 1, from cement grade 400 in Fig. 2.
Back to index
Problems arising from incorrect proportions in the manufacture of concrete structures
The most common problem in the construction of concrete structures is the cracked surface. Its main reason is that the proportions of the constituent components of concrete were incorrectly selected. Therefore, when starting to prepare a mixture, it is necessary to know exactly how each component affects the properties of concrete.
In concrete mortar, water is responsible for the density. In excessively liquid concrete, there is a lot of dissolved air, and therefore the components are unevenly mixed. As a result, cement milk flows down the pour during work. At the same time, the created structure weakens, and its surface bursts. Due to the cracked surface, the rubble inside the liquid solution settles down, and the sand, which cannot take large loads, is located at the top.
Thick concrete is very good for construction, but it is quite difficult to get it under normal conditions. In factories for its manufacture, vibrators and vibrating tables are used, with the help of which the constituent components are evenly distributed throughout the volume of the mixture. The delivery of such concrete to the construction site is expensive.
During the construction of private houses, concrete is usually made using a concrete mixer. It is necessary to ensure that the consistency of the solution is neither too thick nor too liquid. You need to tamp it with a vibrator or a stick.
Theoretically, the optimal amount and proportions of water and other components for an ideal consistency are clearly defined. In practice, things are usually not so simple. The problem may arise due to the fact that water can be present in both gravel and sand. Also, during the pouring of concrete or during preparation, there may be increased humidity on the street, it may rain. This can lead to the fact that when the optimal amount of water is poured into the mixture, the concrete will turn out to be liquid. Therefore, it must be taken into account that all formulas and exact proportions are prescribed for the use of concrete mix in rooms with a constant level of humidity. As a guideline for determining the amount of water, the amount of cement is usually taken: for one bucket of cement, you need to use a little less than a bucket of water. In this case, the concrete mixture should be of medium density and in no case liquid. If you use liquid concrete, then after drying it will definitely burst. If, after pouring, cracks began to appear on the surface, they can be repaired with a trowel before the concrete has completely hardened.
Water should be used clean, drinkable, odorless and free of impurities. The future characteristics of the foundation and the setting rate of the cement will directly depend on the quality of the water. To check the quality of water, you need to evaluate its smell and transparency. Best to use in summer cold water, and in winter - heated to 40 ° C.
Crushed stone also plays an important role in the preparation of mortar. It is very important to prepare a mixture in which crushed stone of one fraction will be used. If small and large gravel are poured into the mixture at the same time, then it will be heterogeneous, and the quality is very low. During construction, it is better to use large fractions of crushed stone. Fine crushed stone is also suitable, but it will need to be added in large quantities, while reducing the amount of sand. If fine gravel is not enough, then cracks may appear on the surface.
During the mixing of the mixture during preparation, each pebble of gravel should be covered with a solution of cement and sand - this will give the concrete rigidity. If the solution is not enough or if the components are unevenly distributed, then the concrete will not be able to withstand the necessary loads. Too much solution can also damage the quality. Too greasy concrete may begin to burst.
The quality of sand and its proportions in the mixture affect the quality of the finished product. building material. When choosing it, you need to pay attention to how much clay is contained in the sand. Great content clay indicates the low quality of the sand.
You should be aware that any foreign impurities in the components will have a negative impact on the properties and quality of the future concrete. To check their purity, you can, for example, take a small amount of sand or gravel and pour them into a three-liter jar, add water and mix well. If after a day the water is slightly cloudy or completely transparent, and there is no foreign composition (clay, silt) on the surface of the sand, then the material is suitable for concrete preparation.
Concrete preparation is a very important construction process. The strength of future structures and their performance characteristics depend on the correctness of its implementation and the use of all components in the right proportions. Next, we will talk about right choice components and what proportions of concrete are best used when making concrete yourself.
The main components of the concrete solution
To obtain a high-quality concrete solution, it is necessary to choose the appropriate components for its manufacture, which are determined by the requirements for the strength of the future foundation. We’ll talk about how to prepare a solution for certain tasks a little later, but now let’s figure out what components can be in the solution:
- Cement of a certain marking.
- Sand.
- Various admixtures or plasticizers.
- Stone filler.
- Water.

The choice of concrete elements must be treated responsibly and take into account their features.
Cement
Cement is the main component of the concrete mixture, which is a binder for all elements. When choosing its brand, it is necessary to determine the level of load that will act on its surface, as well as the impact of external destructive factors.
The load force per 1 cm² is indicated on the label immediately after the letter M. For example, for the preparation of the main foundation of structures that are erected during private construction, experts in the construction industry recommend using M500 concrete. This means that 1 cm² can withstand a load of 500 kg on its surface. It is also allowed to use the M400 brand, but such a base will be less durable. For work inside structures, concrete with weaker strength indicators (M300, etc.) is used.
Some rules for choosing cement:
- It should be dry and loose. Do not buy cement of dubious origin, which is lumpy or obviously damp.
- The packaging must be marked. Without it, you may be sold a composition of fake content that does not meet the declared characteristics, which will lead to backfire(from the crackling of the walls to the destruction of the building, due to the destruction of the foundation).
- Pay attention to the numbers after the letter D. The digital equivalent is equal to the percentage of impurities present in the cement. For example, if M300-D40 is written on the package, this means that up to 40% of additional substances are in the binder. For personal use, it is better to purchase options with a value after the letter D, ranging from 0 to 20. This will allow you to get the highest quality solution.
There is one more small rule - buy cement for a certain period before the start of construction work (about 14 days). He needs time to "rest".
Sand
Sand is a component used as a filler for the space formed between coarse concrete particles. Such filling is used to obtain concrete of the highest strength.
Features of his choice:
- The cleaner it is, the better. The same strength of all particles, which cannot be said about sand with the remains of vegetation or earth, improves the quality of the foundation.
- For the manufacture of the mixture, sand is selected, the dimensions of the elements of which are about 2-5 mm. If they differ in size, it should not exceed 2 mm.
- If possible, use sand extracted from the bottom of the rivers. Its quality indicators are optimal for use in construction purposes.
For getting concrete structure with maximum strength, instead of ordinary sand, artificial sand is used - a stone that has been crushed to a small fraction.
impurities
The preparation of the solution sometimes implies the presence of additional components:
- plasticizer. Makes the mixture more fluid or viscous.
- reinforcing substances. Slightly increase the tensile strength of concrete.
- Lime. When adding this component, the solution becomes more pliable for laying and leveling.
- Additives. They can change the characteristics of concrete, allowing it to set in wet conditions or when exposed to critical temperatures.
To use impurities in the manufacture of high-quality concrete, you need to clearly know the proportions and all the subtleties of their use, so if the work is done independently, it is better to refuse them.
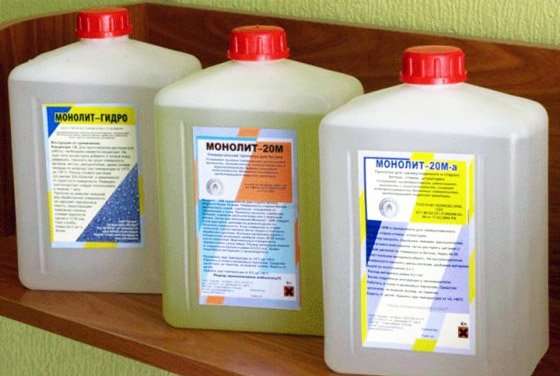
Filler
Key points when choosing crushed stone or gravel:
- The material should be as free from impurities as possible.
- The high surface roughness of the elements improves the strength characteristics of concrete (there will be better adhesion of the elements).
- In the case of a filler, the greater the difference in particle size fractions, the better.
If the filler is stored on the soil, do not use its bottom layer. Along with it, dirt or earth can get into the solution.
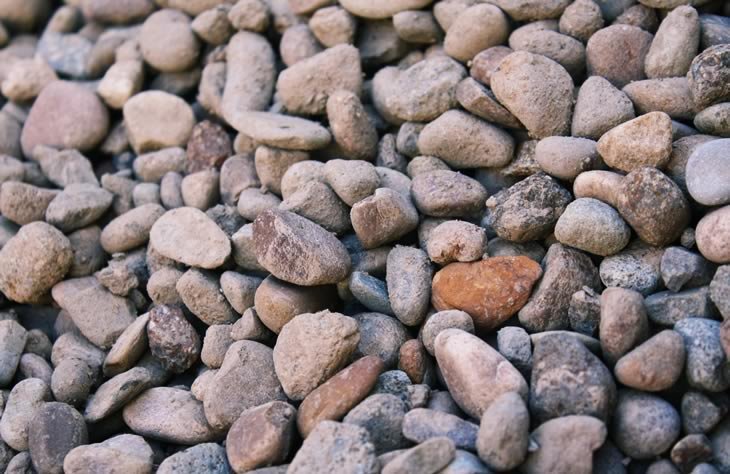
Water
The statement that for concrete there is no difference what kind of water is used is obviously erroneous. If its composition contains components that violate the structure of the elements of the concrete mixture, then it is better to refuse it. The list of such waters includes river or lake.
Important! If the water is drinkable, it is ideal for making concrete mix.
The correct proportions of concrete
The ratio of the components used to each other affects the strength of the final substance. The required level of strength depends on the goals: you need to build the foundation of a building, a small structure, an alley, etc. For example, the foundation for a house should contain required amount crushed stone or gravel of a large fraction, and in the simplest form of a solution, there may be no gravel at all (only cement and sand).
The proportion that has gained the greatest distribution implies a consistent increase in the number of components in geometric progression: 1 part of concrete, 3 of sand, 6 of aggregate. Water should be present from 0.5 to 1 part. Its quantity depends only on the required consistency, which the solution should be obtained.
Such ratios are rather conditional - they do not take into account the sizes of the fractions of the components, as well as their characteristics. Therefore, without exact calculations, a rather unexpected result can turn out.
How to calculate the amount of concrete?
An example of calculus is given in specific example. We need to make 10 cubic meters of the mixture. We use the following components:
- 1 part of cement M500.
- Water 2 parts.
- Aggregate. 4 parts. We will use crushed stone as a filler.
It turns out that you need to make 10 cubes from 7 parts. Each piece will be equal to 1.42 cubes (10 / 7). To find out the volume of each element, you need to multiply the number of its parts by the resulting value. For example, the placeholder will be 4 parts: 4 x 1.42 = 5.68 cubes.

Attention! It is believed that the optimal amount of water used should be equal to half of the cement used.
Preparing concrete is a fairly simple construction process that you can do yourself. But it is important to accurately calculate the proportions, and use only high-quality materials for manufacturing. An inattentive attitude or errors in the preparation of the mixture can lead to subsequent deformation of the building frame, caused by the destruction of the foundation.
What are the proportions for concrete updated: December 14, 2015 by: crunch0
Building a foundation is not an easy task and requires certain skills and knowledge. To obtain high-quality concrete, it is necessary to strictly observe the technology, as well as adhere to general recommendations on the composition and proportions of concrete. Most often, concrete is made from cement grades M-400 and M-500 with the use of sand, crushed stone and sometimes various additives, including antifreeze.
Calculation of concrete proportions
When calculating the proportions of concrete, it is necessary to take into account many factors, for example, fractions of sand and crushed stone, their density, the required qualities of future concrete, namely frost resistance, water resistance, mobility, and others.
The table of concrete proportions shows averaged data. The ratios between materials are usually established by weight or by volume. In this case, the weight (volume) of cement is taken as a unit, and the amount of other components of concrete is expressed as a number of weight or volume of cement.
For example, if a batch requires 25 kg of cement (C), 75 kg of sand (P), 125 kg of crushed stone (S), then their ratio for the composition will be expressed as follows: 25:75:125 = 1:3:5 (by weight). The amount of water is usually expressed in parts by weight of the cement. If the given concrete composition requires 12.5 liters of water, then the water-cement ratio (W / C) will look like this: W / C \u003d 12.5:25 \u003d 0.5. The strength of concrete increases as a result of the interaction of cement with water, which normally takes place in warm and humid conditions.
The interaction of cement with water stops if the concrete dries out or freezes ahead of time, which irreparably worsens its structure and properties. Therefore, concrete needs care that creates normal hardening conditions, especially in the initial period after laying (up to 15-28 days).
In the warm season, the moisture in the concrete is preserved by watering and sheltering. A bituminous emulsion is applied to the surface of freshly laid concrete or it is covered with polyethylene and other films. Concrete under normal hardening conditions has a low initial strength and only after 7-14 days acquires 60-80% of branded strength.
Areas of application of concrete
M-100(B 7.5) Mainly used when carrying out preparatory work before pouring monolithic slabs and foundation strips. We are talking about the so-called concrete preparation: a thin layer of concrete of the lowest grade, specifically M-100, is laid on a sand cushion, and only then, after this layer has hardened, they begin to carry out reinforcing work. Skinny concretes of this brand are used in road construction, as a concrete pad and for installing curbs.
M-150(B 12.5) Mainly used during preparatory work before pouring monolithic foundation slabs. Also, concrete of this brand can be used in the manufacture of screeds, floors, foundations for small structures, concreting paths, etc.
M-200(B 15) It is mainly used in the manufacture of hollow concrete screeds, foundations, blind areas, paths, etc. One of the most commonly used concrete grades. In individual construction, the strength of concrete grade M-200 is quite sufficient to solve most construction tasks: strip, slab and pile-grillage foundations, manufacturing concrete stairs, retaining walls, platforms, paths, blind areas, etc. At reinforced concrete factories and reinforced concrete plants, FBS foundation blocks are made from concrete of this brand, road slabs etc.
W/C values for concrete mixed with gravel. Note: if crushed stone is used instead of gravel, then 0.05 should be added to the found W / C value.
M-250(B 20) Mainly used for making monolithic foundations, incl. tape, slab, pile-grillage; concrete blind areas, paths, platforms, fence tapes, stairs, retaining walls, lightly loaded floor slabs, etc. It occupies a specific intermediate place between the more popular concrete grades M-200 and M-300.
M-300(B 22.5) It is mainly used for the manufacture of monolithic foundations: tape, slab, pile-grillage; blind area, paths, fence tapes, stairs, retaining walls, floor slabs, monolithic walls, etc. Concrete M-300 (B 2Z5) is also the most frequently ordered brand of concrete.
M-350(B 25) It is mainly used for the manufacture of monolithic foundations, pile-grillage reinforced concrete structures, floor slabs, columns, crossbars, beams, monolithic walls, pool bowls and other critical structures. The most used concrete in the production of reinforced concrete products. In particular, airfield road slabs are made from structural concrete M-350, designed for operation under extreme loads. Hollow-core floor slabs are also produced from this brand of concrete. M-350 concrete is the most popular brand of concrete in modern commercial construction.
M-400(В 30) It is mainly used for the manufacture of bridge structures, hydro-technical structures, bank vaults, special reinforced concrete and reinforced concrete products: columns, crossbars, beams, pool bowls and other structures with special requirements. Concrete M-400 (B 30) is a fairly rarely used brand of concrete. As a rule, the use of such concrete is regulated by special requirements related to the conditions of further operation. reinforced concrete structures made from such concrete. In private construction, it is practically not used for a number of reasons:
- the strength of concrete grade M-400 (B 30) is much higher than may be needed in domestic low-rise construction;
- accelerated concrete setting time is fraught with serious problems during: long-distance delivery and sluggishness of builders who accept concrete, who do not have time to lay it, and as a result, an unbreakable concrete block on the site;
- the high cost of such grades of concrete due to the high content of cement. The production of M-400 concrete is permissible only on crushed granite. More often with the use of plasticizers and other special additives in concrete.
M-450(B 35) It is mainly used for the manufacture of bridge structures, hydraulic structures, special reinforced concrete structures, columns, crossbars, beams, bank vaults, subways, dams, dams and other structures with special requirements. In private construction, it is practically not used.
M-500(550) (B 40) It is used for the manufacture of bridge structures, hydraulic structures, special reinforced concrete structures, columns, crossbars, beams, bank vaults, subways, dams, dams and other structures with special requirements. In all recipes, passports and certificates, it is designated as M-550 concrete. In vernacular, the figure of 500 has strengthened behind him for reasons unknown to anyone. Does not apply to private construction.