To estimate the cost of building a private house or non-residential structure, it is necessary to accurately determine the required amount of material used in construction. One of the most common and popular materials for the construction of load-bearing internal and external walls, as well as partitions, is the foam block. There are two ways to calculate the required number of foam blocks - using an online calculator, or using your own calculations.
Calculation using an online calculator
Using this calculator, you can calculate the required number, as well as the parameters of the foam blocks used in the construction of walls in private houses and other structures. This takes into account the openings reserved for windows and doors, as well as the possible presence of facades. In addition, this calculator allows you to determine the weight, volume and price of the blocks used, the amount of cement required for the joints, the area of the reinforcing mesh and other building materials.
Calculator
For accurate volume information building material all data must be filled in as completely as possible. First of all, you need to specify the parameters of the foam block used - its dimensions and density. Then fields are filled in with information on the dimensions of the structure itself - the length, height and thickness of the walls, as well as the parameters of related materials (mortar thickness, frequency of the masonry mesh). Knowing the price of one cube of foam block, you can calculate the total cost of all building material.
Calculation results
After filling in all the data, and clicking on the "calculation" button, the online calculator will display the following data:
- The perimeter of the building is the exact length of all the walls of the building, taking into account the thickness of the foam block;
- Total masonry area - openings for window and door openings are taken into account;
- Wall thickness - a parameter depending on the type of masonry, as well as the thickness of the cement joint;
- Number of blocks - the total number of foam blocks in pieces;
- The total weight of the blocks - does not take into account the mass additional materials(reinforcing mesh, solution), allows you to choose the best delivery option;
- The amount of mortar for the entire masonry - the total volume of cement mortar;
- The number of rows, taking into account the seams - when calculating the gable is not taken into account;
- The amount of masonry mesh. The mesh provides reinforcement of the wall structure, increasing its strength characteristics. The default is to use a grid on each row;
- Approximate weight of finished walls - the weight of blocks, mesh and cement is taken into account;
- The load on the foundation from the walls is a parameter that allows you to determine the parameters of the foundation. The calculation does not take into account the weight of the roof, insulation and finishing materials.
Using this calculator, you can also determine the required amount of building material for interior partitions. To do this, you need to reset all data on the bearing walls, and enter the parameters of the partitions. Add up the results for the two calculations.
Independent calculation of the number of blocks
Unfortunately, the online calculator does not always allow you to take into account all the parameters of the structure, and you need to do the calculations yourself. To do this, you need to know the dimensions of the house and internal partitions, the thickness of all walls, the dimensions of the openings for doors and windows. Given the fact that foam blocks are perfectly processed, almost all cut pieces can be effectively used in construction. However, the reserve for the battle should still be done.
Foam blocks today are presented in a huge assortment, and differ both in their overall dimensions and in strength characteristics. The choice of one or another type of block, as well as the type of masonry, depends on the required thickness of the walls in the building. There are several ways to carry out laying - on a bed, or block spoons, in 1, 1.5 and 2 blocks. In the construction of external walls, internal load-bearing walls, as well as partitions that are not under load, should be used different kinds blocks, or laying methods.
For the construction of external walls, foam blocks are most often used, with a size of 600x300x200mm or 600x400x200mm. Any masonry can be used, but the total wall thickness should not be less than 300 mm. For internal walls that are loaded from the side of the roof, exactly the same blocks are used. As a material for interior partitions, foam blocks are most often used, 600x300x100mm in size, laid on a spoon. The thickness of the wall is 100mm.
Given these dimensions, it is easy to calculate that one block used for the construction of load-bearing walls occupies a volume of 0.036 cubic meters, and for partitions - 0.018 cubic meters. Knowing the dimensions of the walls (thickness, width and height), you can calculate their volume. Further, dividing this number by the volume of one block, we obtain the total number of blocks for each wall. If there are window or door openings in the wall, find out their total volume and subtract from the result.
Also, when calculating the volume of blocks required for the construction, it is necessary to take into account the thickness of the cement joint. To do this, you should know the number of blocks along the height and along the length of the wall. To obtain the volume of mortar between rows, it is necessary to multiply the number of these rows by the thickness, total length and width of the joint. To find out the volume of cement along the length of the wall, multiply the same dimensions of the seam by the number of blocks that fit in one row. Sum up the received data. After that, the total volume of the seams is subtracted from the volume of the walls.
The same manipulations are carried out with internal load-bearing walls and partitions. To the total resulting number of foam blocks, we add 5-7% for the battle during construction, and about 3% for damage during transportation (may be absent altogether).
An example of calculating the number of foam blocks
Suppose that we are faced with the task of building a house from a foam block, which has the following overall dimensions: 10x7x3 m. The house has one room (no internal partitions), there is one door (2x0.9m) and three windows (1.3x1.5m each) . The thickness of the walls should be 30 cm, and the thickness of the seams vertically and horizontally - 5 mm each. It is necessary to determine the required number of foam blocks for the construction of such a house.
As a material, we choose foam blocks, 600X300X200mm in size, because. the thickness of the walls should be 30 cm. Next, you need to calculate the total area of \u200b\u200bthe walls. To do this, we find the perimeter of the outer walls 7 + 7 + 10 + 10 \u003d 34 sq.m and multiply this number by the height of the wall (3m) - 34x3 \u003d 102 sq.m. At the same time, we did not take into account that the house has three more windows and a door. Therefore, we find the area of these openings - 3x (1.3x1.5) + (2x9) \u003d 7.65 sq.m. Subtract from total area walls area of openings - 102-7.65 = 94.35 sq.m.
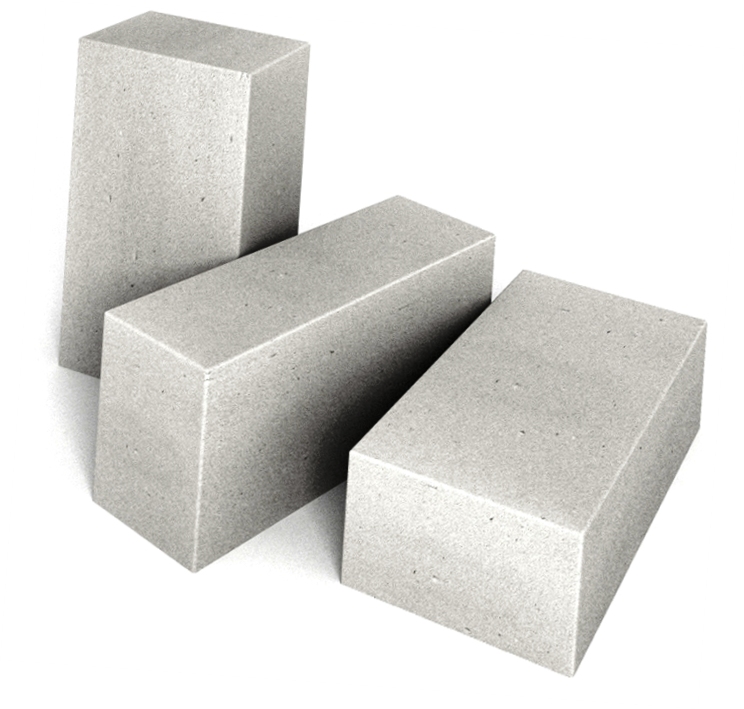
Given the fact that only walls of the same thickness are used in the calculation, there is no need to find their volume. It is enough to find out only the area of one foam block, taking into account the thickness of the cement joint, and then divide the total area of \u200b\u200bthe house by this number. So, the outer area of the foam block, taking into account the seam, is - (0.6 + 0.005) x (0.2 + 0.005) \u003d 0.125 sq.m. The total number of required blocks is 94.35 sq.m / 0.125 sq.m = 755 pieces.
We multiply the resulting number of blocks by 8% (combat and marriage during transportation), we get 816 blocks. This example is elementary, because it involves only external load-bearing walls, and also masonry is used in one block. If the house had internal walls and partitions, they could be calculated separately.
Knowing the required number of foam blocks and their parameters, it will not be difficult to calculate their volume, weight, and also the number of pallets. In accordance with these data, it will be possible to choose the most optimal type of transportation.
Material calculation
WALLS: | |
expanded clay concrete (390x190x188mm): | |
38.98 m³ x 3300 rub/m³ | 128634 rub. |
reinforced concrete jumpers 2PB 17-2-p (1680x120x140): | |
12 pcs. x 462 rubles / pc. | 5544 rub. |
reinforced concrete jumpers 2PB 13-1-p (1290x120x140): | |
11 pcs. x 383 rub./pc. | 4213 rub. |
reinforced concrete jumpers 2PB 10-1-p (1030x120x140): | |
6 pcs. x 357 rub./pc. | 2142 rub. |
masonry reinforcing mesh (50x50x3 mm): | |
32 m² x 102 rubles/m² | 3264 rub. |
extruded polystyrene Penoplex 35: | |
0.1 m³ x 5100 rub/m³ | 510 rub. |
flexible reinforcement BPA 4-2P 300mm with insulation clamps: | |
420 pcs. x 3.3 rub./pc. | 1386 rub. |
front single brick: | |
4394 pcs. x 13 rubles / pc. | 57122 rub. |
sand-cement mortar: | |
5.8 m³ x 2700 rub/m³ | 15660 rub. |
: | |
8.45 m³ x 3700 rub/m³ | 31265 rub. |
TOTAL: on the walls | 249740 rub. |
FOUNDATION: | |
sand: | |
3.6 m³ x 850 rubles/m³ | 3060 rub. |
foundation blocks FBS 24-6-6: | |
32 pcs. x 4665 rub./pc. | 149280 rub. |
sand-cement mortar: | |
1.7 m³ x 2700 rub/m³ | 4590 rub. |
concrete M200: | |
16.2 m³ x 4200 rub/m³ | 68040 rub. |
armature D10-12 AIII: | |
1 t x 37,500 rubles/ton | 37500 rub. |
pine board for formwork: | |
0.5 m³ x 6500 rub/m³ | 3250 rub. |
roofing material RKK-350: | |
5 rolls x 315 rubles/roll (10m²) | 1575 rub. |
TOTAL: on the foundation | 267295 rub. |
COVERS: | |
floor beams Ytong 200: | |
92 l.m x 959 rub./l.m | 88228 rub. |
embedded blocks Ytong D500: | |
12.2 m³ x 5570 rubles/m³ | 67954 rub. |
reinforcing mesh 100x100x5.0: | |
69.9 m² x 110 rubles/m² | 7689 rub. |
bar fittings Ø12 AIII: | |
0.3 t x 37500 rub/ton | 11250 rub. |
concrete M200: | |
7.2 m³ x 4200 rub/m³ | 30240 rub. |
mineral insulation (Rockwool): | |
0.3 m³ x 3700 rub/m³ | 1110 rub. |
TOTAL: by floors | 206471 rub. |
ROOF: | |
wooden beams (150x50mm): | |
1.6 m³ x 7000 rub/m³ | 11200 rub. |
antiseptic solution: | |
24 l x 75 rubles/liter | 1800 rub. |
waterproofing film (Tyvek Soft): | |
94 m² x 68 rubles/m² | 6392 rub. |
bituminous euroslate 2000x950x2.7: | |
54 sheets x 399 rubles/sheet | 21546 rub. |
roofing nails 73x3mm: | |
12 pack. x 190 rubles / pack (250 pcs.) | 2280 rub. |
corner ridge (1000mm): | |
10 pieces. x 290 rub./pc. | 2900 rub. |
lathing board 100x25mm: | |
0.7 m³ x 7000 rub/m³ | 4900 rub. |
10:0,0,0,220;0,290,220,220;290,290,220,0;290,0,0,0|5:163,163,0,220;0,163,103,103;163,290,152,152|1134:212,152|1334:138,35;138,114|2255:0,125|2155:64,0;64,220;201,220|2422:290,55;290,98|1934:203,-20
RUB 836,074.0
Only for the Moscow region!
Calculation of the cost of work
Do you want to know how much it costs to build your house and choose contractors?
Place an express application and get offers from professional builders!
An example of a layout of 8x6 m for calculation |
Structural scheme |
|
![]() |
1.
Expanded clay block d=400mm; 2. Brick face d=120mm; 3. Mineral wool plate d=100mm; 4. Air gap d=20-50mm; 5. Reinforced concrete screed h=200mm; 6. Insulation foam d=30-50mm; 7. The overlap is prefabricated-monolithic; 8. Ondulin roof; 9. Foundation tape block h=1.8m; |
Expanded clay block wall with brick facade and internal insulation
Claydite-concrete block masonry
In appearance, these are comfortable, volume: 390/190/90 and 390/190/188, wall stones, produced according to the recipe for volumetric vibrotamping from expanded clay concrete composition.
The main difference between expanded clay concrete is its excellent hydrophobic characteristics: in an environment with 100% humidity, cement-expanded clay material absorbs moisture 200% less than foam concrete. This is of great importance because the hygroscopicity coefficient seriously affects the thermal insulation properties of the wall in a real-life environment.
The thermal conductivity of expanded clay concrete masonry is one and a half times lower than that of a facade made of perforated bricks of the same section, at a comparable selling price.
Expanded clay blocks have gained quite wide recognition for private development due to fire resistance, manufacturability and hygiene. In the states of Europe: Finland, Czech Republic, the Netherlands, Norway, Germany, Sweden, at least 40 percent of buildings were built from expanded clay.
- Due to the fact that the diffusion of steam through the brick is stronger than that of expanded clay concrete, the ventilated gap between the expanded clay concrete blocks and brickwork(in the absence of a heat-insulating layer of mineral wool) is not performed.
- An experienced worker lays out about 3 cubes of expanded clay blocks per shift, which is 3 times more than the intensity of brick work, and the savings cement mixture increases to 50-60%.
- Due to the fact that, for a comfortable stay, 40 cm of expanded clay concrete is not enough, the best solution would be to insulate the block wall with a rigid basalt fiber thermal screen (for example, type: Isover, PZh-200, P-125, Ursa, Izomin, Izorok, Knauf , Rockwool, P-175), with a layer of 0.1 m, with further installation (through the ventilation gap) of a protective and decorative shell. In this way, a gas-permeable structure is obtained, which makes it possible for the structure to get rid of excess moisture.
- If the insulating layer in the multilayer wall is a “non-breathing” extruded foam, for example, such as: Ursa XPS, Teplex, Polyspen, Styrodur, Technoplex, Styrofoam, Primaplex, Penoplex, it makes no sense to leave a blown gap between the brickwork and expanded clay concrete blocks, but it will be necessary to install a vapor barrier layer from the side of the rooms and, moreover, plan a complex of forced ventilation (and, better, air heating).
- On the upper row of expanded clay concrete blocks, in a wooden formwork form, a reinforced w / concrete pour is made, 200 mm thick. On the facade surface, the reinforced concrete belt is heat shielded with a 5 cm layer of extruded polystyrene foam.
brick cladding
The most well-known building material for building walls is, of course, facing brick, which, in addition to wealthy appearance, has a large (up to 100 freeze-thaw cycles) frost resistance and insignificant (about six percent) water absorption, which leads to a long period of operation of brick buildings. Among the front clay brick materials, in addition to standard, clinker, figured and glazed bricks are produced.
Nowadays, facing bricks of various profiles (beveled, rounded, wedge-shaped, rectangular) and reliefs (chipped, corrugated, smooth, rough), as well as colors (from beige to chocolate), are being sold, which allows you to implement any non-standard artistic ideas.
In the case when a variant of a wall with mineral insulation is planned, the significant technological points for the construction of a complex wall are:
- Expanded clay block main masonry with a cross section of 0.4 m is being made on a sand-cement mortar.
- Through three rows of expanded clay concrete blocks and gaps of 1-1.5 m, special basalt fiber fixing rods with a disk holder (type "Galen" BPA-300-6-2P) are placed, for dressing with the front wall, in addition, the corners are reinforced with steel rods walls, support pads of lintels, another five/six rows of masonry.
- Pieces of basalt-fiber thermal protection are put on the protruding rods of the connectors without gaps and pressed with clamps.
- On top of the thermal protection, it also makes sense to install a hydro and windproof film (Tyvek, Izospan, Yutavek).
- In a 1/2-brick, a facing wall is made, which is connected to the expanded clay block masonry with the help of reinforcing outlets made.
prefabricated foundation
Foundation blocks are a traditional building material that allows you to build the foundation of a house in a short time.
Building blocks differ in categories: FBS - solid foundation blocks, FBV - with a groove for communications, FBP - hollow. Usually concrete blocks are made with a height of 550-650 mm, the horizontal size varies within 0.9-2.4 m (FBS-9 ... FBS-24), the transverse size is fixed at 0.3-0.4-0.5-0.6 m.
When building a block foundation on solid and dry geosubstrates, building blocks can be laid directly on a leveled soil base.
On medium heaving lands, it is permissible to install FBS blocks without layer-by-layer reinforcement, however, a reinforced concrete belt 0.10-0.20 m thick with reinforcement d10-d14 is arranged above and below them.
The use of one or another size of the foundation block follows from the thickness of the main walls of the building. For low-rise buildings, a block thickness of 30 - 40 cm is acceptable. The cross section of prefabricated block foundations can be less than the outer masonry of the walls of the house, since they are much more durable.
To expand the area of \u200b\u200bthe support, in order to thereby reduce the likely movements of the underlying layer, the foundation blocks should be mounted on pre-laid concrete pads.
The choice of foundation blocks, as the basis for the construction of the foundation, is often determined by the all-season work or tight deadlines.
Nowadays, the foundation of individual FBS-blocks, according to a range of important characteristics, among which: resistance to lateral loads and cost, gives priority to another option - an all-concrete reinforced foundation base.
When the properties of the underlying layers are not clear, it is better for reliability, instead of ready-made pillows, to prepare a reinforced reinforced concrete screed.
- The installation of foundation supports starts from the corner of the building, while first of all the FL blocks are installed under the external walls, and only then for the internal ones.
- On the bedding (up to 15 cm) of coarse sand or laid out concrete pillows, FBS blocks are placed in a checkerboard pattern, fixed with a sand-cement mortar.
- The installation of concrete blocks is carried out relative to corners, along walls diverging at right angles, guided by a laser theodolite. Ordinary blocks are installed by a truck crane on a leveled layer of cement mixture.
- The assembly begins with the laying of lighthouse blocks at the intersections of the center lines and at the corners of the building. It is necessary to proceed with the arrangement of wall blocks only after controlling the orientation of the signal blocks in plan and in height.
- The geometry in the plan is verified by taking the linear size of the foundation fragments and the size between opposite corners, and the vertical position - by level or spirit level.
- Windows for launching water and sewer pipes to the zero level are made by making a gap between the blocks, followed by brick or mortar.
Prefabricated monolithic ceiling
Prefabricated-monolithic overlap - still quite New Product in the Russian construction market, which includes two main components: aggregate blocks made of porous concrete and concrete beam structures with a free reinforcing cage.
The use of the prefabricated block principle is rational for the installation of interlevel panels in houses with light cellular concrete masonry and columnar-distributed foundation bases, as well as when modifying existing wood-and-beam floors, if the use of conventional reinforced concrete elements is unrealistic.
The installation of the interlevel panel, due to the insignificant weight of the components of the monolithic-prefabricated technology (the mass of the beam run is 13 ÷ 18 kg/r.m., the mass of the spacer block is 6 ÷ 15 kg), is done manually and without the operation of lifting equipment.
Interbeam blocks-spacers, according to the composition of the material, are divided into: solid aerated concrete (Ytong, dimensions: 600x200x250 mm, weight: 15 kg), hollow claydite-concrete (Albert, weight: 12-14 kg, dimensions: 530x200x200 mm), ceramic porous (Porotherm , weight: 22 kg, dimensions: 510x250x219 mm) and hollow polystyrene concrete (Marko, weight: 6 kg, dimensions: 530x200x200 mm).
It should be added that the described method provides for the possibility, in one stage of concreting the interfloor slab, to obtain at the same time a reinforced concrete grillage along the bearing walls. To do this, the beams are hung on racks, with a rise of 5-10 cm from the upper plane of the wall, on which additional reinforcing bars are placed and the sides are attached. At the end of the layout of the filler blocks, the entire structure is poured with concrete.
This technique is very interesting for heat-efficient, however, at the same time, not very strong, walls made of porous blocks: aerated concrete, foam concrete, gas silicate, polystyrene concrete, the construction of which requires a monolithic reinforced concrete grillage for the installation of beam girders.
The usual sequence of work in the construction of a prefabricated monolithic floor:
- Beams are laid out on the horizontal aligned parts of the wall, for sand-cement preparation with a layer of 1.0 ÷ 1.5 cm, with an interval of 62 cm. The length of the supporting section of the beam structure is taken as a minimum of 12 cm.
- At the time of installation of intersupport block fillers and concrete laying, beam structures are placed on distributed, with an interval of 300 cm, and then removed, anchor points from metal pipe racks d Ø40-50 mm or boards with a base of at least 50x100 mm.
- embedded blocks made of aerated concrete, expanded clay concrete or polystyrene concrete, realizing the function of constructive formwork, are stacked with special stampings on top of the beam runs. Due to the fragility of block inserts for bending, for walking on them, it is necessary to build decks from boards 3 ÷ 5 cm or thick plywood.
- At the top of the filler blocks, reinforcement is rolled out in the form of a grid with cells of 10x10 cm from wire Ф 5 ÷ 6 mm, which is attached to the unclosed reinforcement of the beams using annealed wire rod grade d2 Vr-1. The joining of adjacent grids is carried out by overlapping, with a value of at least 10 ÷ 15 cm.
- Next, pour concrete mixture with a layer of 5 ... 10 cm of grade B15 (M200) ... B20 (M250), they are leveled and rammed with a vibrator.
- In the process of hardening of the poured prefabricated-monolithic floor, it must be periodically soaked. It is allowed to dismantle the technological supports only after half a month.
Soft slate roof
Ondulin (also known as soft slate, ondulin slate, bituminous slate, bituminous slate, euroslate) is a molded cardboard sheet impregnated with an SBS-modified bitumen component and colored with a polymeric weather-resistant pigment. bitumen slate is produced with a variety of names: Ondura, Ondulin, Guttanit, Korrubit, Aqualine, Bituvel, Nuline. Typical parameters of canvases: length/width - 2/0.95 m, number of waves - 10.
The main trump cards of euroslate roofing are low cost and ease of installation. Of the significant disadvantages, it is fair to single out a certain flammability of the bitumen-cardboard base, as well as a rather rapid loss of richness of colors, in comparison with a metal roof.
The roof is installed on a load-bearing frame made of rafter beams and board-and-slab lathing.
In the construction of individual buildings, a two- or three-span system is usually performed with inclined rafters and intermediate supporting walls.
The interval between the rafters is within 60 ÷ 90 cm with a width / thickness rafter legs 50x150÷100x150 mm; the lower ends of the rafters are fixed to a Mauerlat beam measuring 100x100 ÷ 150x150 mm.
A typical method for installing a bitumen sheet roof:
- The inter-row overlapping of corrugated sheets of onduline slate and the step of laying the crate preparation are determined by the angle of the roof: when the slope is steeper than 15 degrees, then the pitch of the sheathing is 0.30 ... 0.35 meters, and the overlap is 170 mm.
- In order to prevent the raising of corrugated euroslate sheets during wind gusts, it is recommended to start their flooring from the lower zone of the end cut of the slope, opposite to the prevailing wind direction.
- The above row is carried out with a shift of ½-sheets, from the sheets of the lower level, in order to prevent unnecessary overlap in the joints of four adjacent corrugated sheets, leading to the appearance of cracks.
- Sheets of bituminous slate are nailed along the bottom line into each wave, along 2 intermediate crate bars - into odd upper half-waves, and the top is covered with an overlap of the upper row or the edge of the ridge. To fasten each sheet, you need about 20 self-cutting roofing screws (size 65.0x5.5 mm) or nails: size -73.5,Ø3.0 mm with neoprene washers.
- For one row, the overlapping of the canvases should be arranged in one corrugation, and with a roof angle of less than 10 ÷ 11 degrees - in 2 corrugated waves.
- Strengthening of the ridge elements is carried out in the direction of laying the roofing sheets, overlapping by 200 mm, with nails nailed into each wave crest of the covered corrugated sheet.
- In order to seal the side edges of the pitched surface, chip corners are used, the installation of which is done from the bottom corner, with an overlap of 0.2 m.
It is easy to determine the costs for the selected new building option using the built-in cost calculator.
Online calculator building blocks is designed to perform calculations of building materials necessary for the construction of walls of houses, garages, utility and other premises. The calculations can take into account the dimensions of the gables of the building, door and window openings, as well as related materials such as mortar and masonry mesh. Be careful when filling in the data Special attention for units of measurement.
When filling in the data, pay attention to the additional information with the sign Additional Information
Technologies do not stand still, including construction. For the construction of walls, wood was replaced by brick, and today its place is increasingly occupied by building blocks obtained by artificial means, and, depending on the raw materials used, may have different characteristics.
With building blocks are popular in the construction of low-rise buildings, and walls of monolithic-frame buildings. Of these, you can not only build external walls, but also be used for internal partitions and interior walls. Concrete blocks are also suitable for the manufacture of prefabricated foundations for light buildings.
The advantages of building blocks are obvious. With their help, it is possible to build a building in a short time without the use of special equipment. They have good thermal insulation and the necessary strength. Therefore, the funds spent on insulation will be significantly lower than in brick construction. And if we compare building blocks with wooden log cabins, then this is not only less additional funds and work, but also a higher durability of the building.
Blocks do not need such a strong vapor barrier as, for example, wood. Given their size and lightness, even the foundation for such a house will cost much less compared to brick and reinforced concrete. The use of a special masonry adhesive increases the thermal insulation of the walls, and makes them more attractive in appearance.
Building blocks can be divided into two types:
- artificial - they are obtained by mixing concretes of different composition at factories, using special vibroforming machines. The resulting material, depending on the raw material, is distinguished by the necessary strength, density and thermal insulation properties.
- Natural - are relatively more expensive than those offered by the factory. They are obtained by careful processing, grinding of rocks. Most often they are used as decorative finishes facades.
Artificial building blocks include: aerated concrete, foam concrete, expanded clay concrete, polystyrene concrete, sawdust concrete and many others. Each type is used depending on the required qualities, and has both a number of advantages and a number of disadvantages. One species has good thermal insulation performance, but they are somewhat inferior in strength (when compared, for example, aerated concrete and expanded clay concrete). In any case, buildings built using building blocks require less time to build turnkey houses, compared to the same wooden log cabins, which take a long time to finally dry and settle. And only after that you can begin the final decoration of the room.
When building from blocks, interior decoration premises can be produced immediately after construction is completed.
By design features, building blocks are distinguished into:
- Structural They are used for the construction of load-bearing walls of a building. They have high strength, but also high thermal conductivity and high weight. In this regard, during the construction of residential premises, mandatory additional insulation is necessary.
- Structural and heat-insulating They are used for the construction of load-bearing walls of low-rise buildings. They have average characteristics, both in terms of strength and thermal insulation qualities. Ideal for seasonal residences.
- Thermal insulation They are used for the construction of only self-supporting walls, such as internal partitions and walls of frame buildings, as well as for the insulation of load-bearing walls. They have low thermal conductivity, low weight, but also low strength.
Unfortunately, on this moment there is no ideal material that has high rates of all the necessary characteristics at once, such as low thermal conductivity, high strength, low weight and cost. And in each case, it is necessary to choose exactly the material that is most suitable for the planned construction, taking into account the necessary requirements.
The cost of finished walls is approximately equal to 1/3 of the cost of the entire building.
Further presented full list performed calculations with brief description each item. If you did not find the answer to your question, you can contact us using the feedback located in the right block.
General information on the results of calculations
- Building perimeter - The total length of all walls taken into account in the calculations.
- About total masonry area - Square outside walls. Corresponds to the area of the required insulation, if such is provided for by the project.
- wall thickness - The thickness of the finished wall, taking into account the thickness of the mortar joint. May differ slightly from the final result depending on the type of masonry.
- Number of blocks - The total number of blocks required to build walls according to the given parameters
- About the total weight of the blocks - Weight excluding mortar and masonry mesh. As well as the total volume, it is necessary to select a delivery option.
- Number of mortar for the entire masonry - The volume of mortar required for laying all blocks. Volume weight solution may differ depending on the ratio of components and additives introduced.
- Number of rows of blocks including seams - Depends on the height of the walls, the size of the material used and the thickness of the masonry mortar. Gables not included.
- Number of masonry mesh - The required amount of masonry mesh in meters. It is used to reinforce masonry, increasing the solidity and overall strength of the structure. Pay attention to the number of reinforced rows; by default, the reinforcement of each row is indicated.
- Approximate weight of finished walls - The weight of the finished walls, taking into account all building blocks, mortar and masonry mesh, but excluding the weight of insulation and cladding. - Load without taking into account the weight of the roof and floors. This parameter is necessary to select the strength characteristics of the foundation.
In order to calculate the material for partitions, you need to start a new calculation and specify the length of only all partitions, the thickness of the walls to the floor of the block, as well as other necessary parameters.
Using the online calculator of building blocks, you can determine the amount and volume of building materials needed to build the walls of houses, garages, boxes, baths, country houses and other premises. The calculations may take into account the dimensions of the gables of the building, door and window openings, additional openings (for example, gates), as well as related materials such as mortar and masonry mesh.
When working, pay special attention to the units of measurement of the entered data!
Calculation results
Print Send by emailIf the calculator was useful to you, please click on one or more social buttons. This will help a lot further development our site. Thank you so much!!!
Instructions for working with the calculator
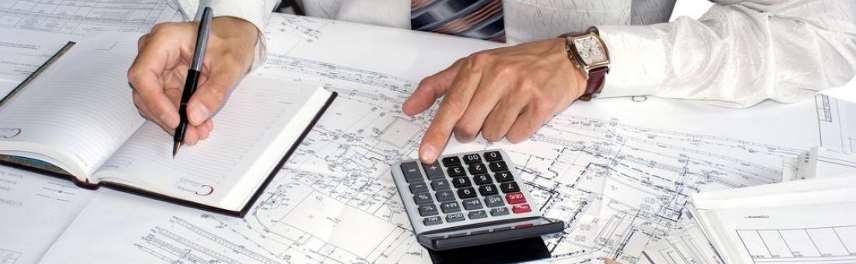
Initial data
Step 1: The calculator is designed to calculate any kind of building blocks. First, set the exact dimensions of the building block, excluding the masonry seam. Be careful here: set the length, width and height of the block relative to how the block will lie in the masonry. Next, enter such building parameters as the height of the wall and the total length of the wall along the outer perimeter of the building.
Step 2: Then specify how the blocks are stacked. The thickness of future walls directly depends on these data. This can be a half-block construction (the wall thickness will be equal to the block width) or a whole block (the wall thickness will be equal to the block length). Choose the laying method depending on the designed number of storeys of the building, the type of floors and other structural features.
Step 3: To make the calculation more accurate, it is necessary to take into account the thickness of the masonry joint, consisting of mortar, or glue and other materials. Sometimes the thickness of the horizontal and vertical seams is different.
Step 4: To calculate the masonry mesh, you need to decide how many rows you will lay it in. Data about it can be omitted, leaving the item "Ignore" in the column. Or count it, indicating that it lies through the Nth number of rows.
Step 5: Block weight is an optional parameter. But if you want to calculate the approximate weight of the finished walls and the load from the walls on the foundation, then it is still desirable to indicate it. Price is also an optional parameter. Specify it if you want to calculate the total cost of the blocks.
Step 6: To take into account the gables of the building, as well as windows, doors and additional openings in the calculations, check the appropriate boxes, and set the necessary parameters in the list that appears.
Step 7: After filling in all the fields, click the "Calculate" button. You can print your results or send them by email.
For convenience, various elements buildings are best counted separately. For example, external walls and interior partitions may differ both in height and in the way the blocks are laid. In this case, carry out two independent calculations.
Interpretation of calculation results
Building perimeter | The sum of the lengths of all walls taken into account in the calculations |
Total masonry area | The area of the outer side of the walls. Equals the area of the required insulation, if it is included in the project |
wall thickness | The thickness of the folded wall, taking into account the mortar joint (s). Minor deviations from the final result are allowed depending on the laying method. |
Number of blocks | The total number of all blocks required to build walls according to the specified parameters |
Total weight and volume of blocks | Net weight and volume of blocks (excluding mortar and masonry mesh). This data may be useful for choosing a delivery method. |
The amount of mortar for the entire masonry | The volume of mortar that will be required to lay all the blocks. Deviations in the indicator are allowed. Depends on the ratio of components and input additives |
Number of rows of blocks including seams | It is determined by the height of the walls, the dimensions of the materials used and the thickness of the masonry mortar. Fronts are not taken into account |
Optimal wall height | The recommended height of the block wall, which should generally be a multiple of the height of the block itself, including the joint. You can agree with this recommendation - then recalculate by setting a new wall height value in the calculator |
Number of masonry mesh | The required amount of masonry mesh in meters. It is used to reinforce masonry, increasing the solidity and overall strength of the structure. |
Approximate weight of finished walls | The weight of the finished walls, including all building blocks and masonry mortar, but excluding the weight of insulation and cladding | Load without taking into account the weight of the roof and floors. This value is needed to select the strength characteristics of the foundation |
Wall building blocks
Not so long ago, a brick house was considered a sign of the great wealth of its owners. Now in the first place when choosing building materials is practicality and pragmatism. Building blocks meet these requirements like no other material. They can be used not only in the construction of external walls, but also for partitions, interior walls.
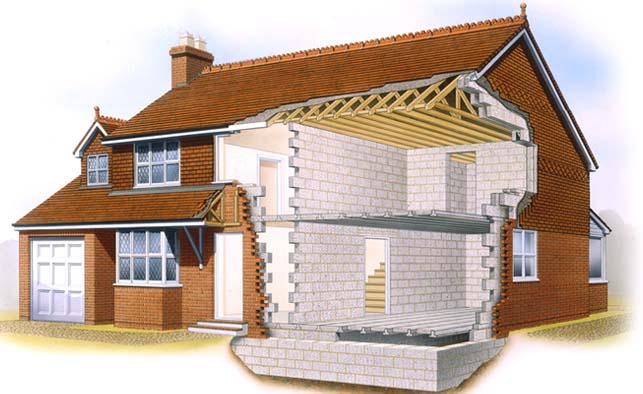
What are the benefits of building blocks?
- Firstly, everyone is attracted by the short construction time and the lack of the need for special equipment.
- Secondly, building blocks are famous for their thermal insulation and durability. Those. Compared to brickwork, the reduction in the cost of insulation will significantly save construction costs. And the strength of the building blocks gives buildings made of blocks a higher durability compared to wooden buildings.
For reference: the cost of finished walls is approximately equal to 1/3 of the cost of the entire building!
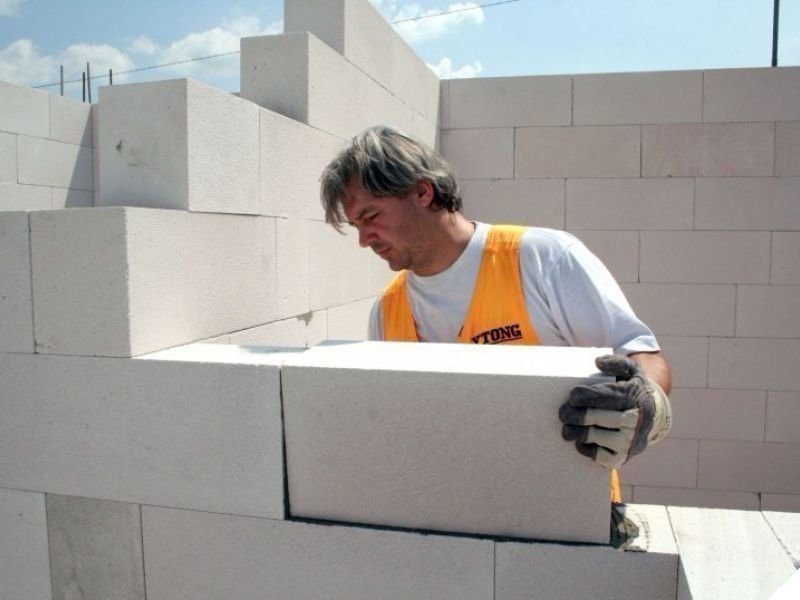
Building blocks are natural and artificial. The first are used mainly for finishing facades. Artificial building blocks are divided into expanded clay concrete blocks, PShchS blocks (based on a sand-gravel mixture), also popularly referred to as cinder blocks, aerated concrete, foam concrete, polystyrene concrete, ceramic, wood concrete and many others.
Each of them is used depending on their advantages and disadvantages. For example, compared to expanded clay concrete, aerated concrete has good thermal insulation, but it is inferior to it in strength.
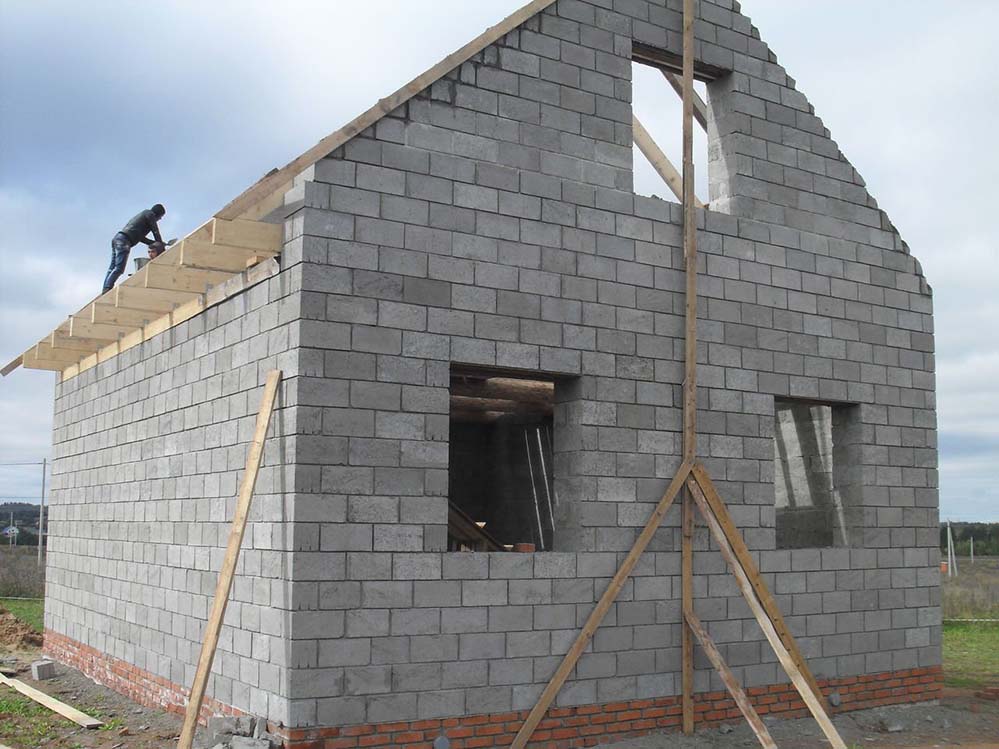
As much as we would not like, but, unfortunately, an ideal material has not yet been invented, which at the same time would have low thermal conductivity, high strength, low weight and cost. Therefore, in each case, it is necessary to choose the material that is suitable for your building. But there is also good news. All blocks have one big advantage: they can be finished immediately after construction is completed, without waiting for drying and settling.
© 2014-2016 website
When building your own house, you often have to deal with a situation where there is either not enough building material, or there is too much of it. Expanded clay concrete blocks are no exception. And despite their relative cheapness, extra costs are always not very pleasant.
There are even situations when a person, saving his precious time, tries to make a quick calculation with the help of building calculators that promise to accurately calculate the number of expanded clay concrete blocks he needs. But in the end, there is still a lot of surplus, or, which is sometimes much worse, there is not enough of them.
Why the calculation of blocks by "construction calculators" is not always accurate
In view of their primitiveness, most construction calculators are primarily intended for an approximate or preliminary calculation of building material, and in most cases are not suitable for an accurate final calculation.
As a rule, calculators work on very simple principle- calculate the area of all walls, subtract the area of \u200b\u200ball windows and doors (some do not even take this into account), and then calculate the number of required blocks, ignoring many factors, such as the presence of gables, the need for armored belts, internal load-bearing walls, the multiplicity of the height of the walls blocks, etc.
What must be taken into account for the accurate calculation of expanded clay concrete blocks
- The most common mistake in calculating expanded clay concrete blocks (KBB) for a house is that many people forget about the gables and do not take them into account. By the way, most online calculators make the same mistake.
- Very often, in addition to the external load-bearing walls, there are also internal load-bearing walls in the house, which will also be laid out from ordinary blocks.
- If your house is faced with brick from the outside, then this must be taken into account, because. in this case, the length of the wall of expanded clay concrete blocks will be slightly less outer wall at home.
- If an armored belt is arranged over the walls, then when calculating the blocks, its height must be subtracted from the total height of the wall.
- The height of the wall of expanded clay concrete blocks, as a rule, should be a multiple of the height of the blocks themselves, together with the seam. Because the height of the block with a seam is about 0.2 m, then the height of the wall without the armored belt should be a multiple of this value (for example, 2.4, 2.6, 2.8, 3.0, etc.).
- The length of the wall will not always be a multiple of the whole number of blocks, i.e. in most cases, there will be not only whole blocks in the wall, but also various inserts, for example, half a block, a quarter, etc. Due to its fragility, it is not always possible to cut or split an expanded clay concrete block without waste.
- It often happens that when unpacking a pallet with blocks, broken blocks are already found there, which will be unsuitable for masonry.
- If lintels will be mounted above the windows and doors, then they must also be subtracted from the total area of \u200b\u200bthe walls, although if the area of \u200b\u200ball the windows is not very large, this is usually neglected.
At first glance, the calculation is going to be very complicated and one cannot do without higher mathematics, but this is only at first glance. In fact, there is nothing complicated here, and I will now prove this with a small example.
An example of calculating blocks for a private house
For example, let's take a small one-story house with two gables, and one internal bearing wall. The thickness of the outer walls is 19 cm (0.5 blocks), the thickness of the internal load-bearing wall is 39 cm (1 block). Outside the house will be faced with brick. A diagram of this house can be seen below.
On the sizes of blocks from expanded clay concrete I will not stop, I have already written in detail about this earlier.
It should be noted that the diagram shows the dimensions of the outer walls, taking into account the facing bricks, in meters. Part of the wall will be occupied by brick and insulation, so each of the outer block walls will be about 15 centimeters smaller on each side.
Calculation of expanded clay concrete blocks for walls without gables
The calculation begins, as a rule, with the determination of the perimeter of the walls of expanded clay concrete blocks. When calculating, everything should be taken into account - all ledges, hallways (if any), balconies, etc.
In our case, each wall will be 0.3 meters less than in the diagram (as mentioned above, due to the fact that part of the wall will be occupied by facing bricks and wall insulation).
Perimeter of all walls: 9.7 x 4 = 38.8 m.
1. It is necessary to determine how many blocks will be in one row around the entire perimeter:
38.8 / 0.4 = 97 pcs.(0.4 is the length of one block along with the seam).
2. The resulting value is multiplied by the number of rows, which depends on the height of the walls (2.4 m = 12 rows, 2.6 m = 13 rows, 2.8 m = 14 rows, etc.). In our case, we take the height of the walls equal to 2.8 m, which corresponds to 14 rows of laying claydite-concrete blocks:
97 x 14 = 1358 pcs.
3. Now you need to subtract windows. We have 2 windows measuring 1.6x1.4 m. Let's calculate how many blocks our windows will replace. Length: 1.6 / 0.4 = 4 pieces, height: 1.4 / 0.2 = 7 pieces, total:
7 x 4 = 28 pcs each box.
Two windows - 28 x 2 = 56 pcs.
4. Entrance doors we have a size of 2 x 1 m. According to a similar scheme:
(1 / 0.4) x (2 / 0.2) = 25 pcs.
5. Subtract doors and windows from the total number of blocks:
1358 - 56 - 25 = 1277 pcs.
Thus, we calculated expanded clay concrete blocks only for external walls, now it is necessary to calculate the internal load-bearing wall, given that its thickness is twice as large, i.e. in the length of one block (39 cm).
Calculation of the internal load-bearing wall of expanded clay concrete blocks
The required number of expanded clay concrete blocks for the inner wall is calculated according to the same scheme, except that now we take one block not 0.4 m, as in the previous calculation, but 0.2 m along with the seam, the difference is clearly visible in the photo.
If you have an internal wall (walls) with a thickness of 19 cm, and not 39 cm, as in the example, then its calculation should be carried out similarly to external ones.
1. The length of the wall is 9.2 m. Let's calculate the number of blocks in one row:
9.2 / 0.2 = 46 pcs.
2. Multiply by the number of rows:
46 x 14 = 644 pcs.
3. Door (2m x 1m):
(1 / 0.2) x (2 / 0.2) = 50 pcs.
4. Subtract the door:
644 - 50 = 594 pcs.
5. Now, by simple addition, we determine the number of expanded clay concrete blocks we need to build a house:
594 + 1277 = 1871 pcs.
I would like to add that if you get a non-integer number when calculating doors or windows, then it is better to round it down to a whole number.
Calculation of gables
Who remembers school course geometry, the calculation of blocks for gables will become a very simple task. To do this, it is enough to know the height of the future pediment, in our case it will be 2 meters. The width of the pediment will be equal to the width of the wall, in our case - 9.7 m.
The area of two pediments is equal to the area of one rectangular wall, in which the lengths of the walls are equal to the width of the pediment and its height.
In other words, we need to find the number of blocks for a wall with a height of 2m and a length of 9.7m:
(9.7 / 0.4) x (2 / 0.2) = 242.5 pcs.
It must be taken into account that the masonry of the pediment, as a rule, begins with a whole row, and already from the second row the blocks begin to be sawn. Therefore, to the resulting number, you need to add two whole series
242.5 + 48.5 = 291 pcs.
Given the large number of sawn blocks when laying the pediment, you can safely add a small amount "for cutting". And thus, it would be better to cook 300 pieces on the gables.
So we counted required amount expanded clay concrete blocks per house with two identical gables:
1871 + 300 = 2171 pcs.
It is worth noting that for a more accurate calculation, it is necessary to count each wall separately, because, even in our case, it turned out that 24 whole blocks + 1/4 blocks are needed for each wall. And when cutting or splitting, rarely 4 quarters will come out of one block, due to the fragility of the blocks themselves. And given the above, you need to take a small margin of 5-7%.
As a rule, the stock is taken "up to a whole pallet", and you can check with the manufacturer. And then calculate how many pallets you need.
If suddenly your outer walls are not 19 cm thick (in the floor of a block), but 39 cm (in a block), then their calculation must be carried out similarly to the internal load-bearing wall from our example, or exactly the same as in the example, then multiplying their number on 2.
How many expanded clay concrete blocks in a pallet
To be honest, there is no definitive answer to this question. "How many blocks per pallet does the manufacturer stack?"- You won't find it anywhere. Different manufacturers, different pallets, one might even say different sizes, although expanded clay concrete blocks do not differ in this variety.
Basically, the number of expanded clay concrete blocks in a pallet depends entirely on several factors:
- From the manufacturer, because there are no strict standards, and everyone completes their products as it suits them best.
- From the size of the pallets, the larger the pallet, the more blocks will fit on it, respectively.
- From the weight of the expanded clay concrete block, since this affects the total weight of the pallet, and too much weight, firstly, the pallet itself may not withstand, and secondly, loading and unloading, and the delivery of the blocks itself can be difficult.
Despite this, there are still some figures that are typical for expanded clay concrete blocks, a certain unofficial standard that many adhere to and complete their products by 72, 84, 90, 105 pieces.
In addition to ordinary blocks with a thickness of 19 cm, blocks with a thickness of 12 cm and 9 cm are produced. Such blocks are called partition or semi-blocks.
Blocks with a thickness of 12 cm are stacked approximately 120 pieces per pallet, in turn, blocks with a thickness of 9 cm, as a rule, are placed on one pallet twice as many as ordinary ones, i.e. 144, 168 etc.