A self-built metal profile greenhouse is the most durable, economical, reliable and popular type of structure for growing plants indoors. Such products, with proper care, are durable, do not require large investments during operation. But in order for the greenhouse to really serve for many years and not collapse under loads, it is necessary to competently approach the design and construction.
The article will discuss how to make a greenhouse from a profile with your own hands, we will show you how to make a drawing, what sizes are appropriate, what material to choose, how to bend, how to fix, what type of roof is more practical for construction.
Metal greenhouse - what is important for design
Before proceeding with practical construction, you need to know that a do-it-yourself metal greenhouse can be built from several types of metal profiles:
- A round metal pipe with a diameter of 20-25 mm, a profile with a diameter of 50 mm is sometimes used for vertical racks of the frame, the elements are usually connected by welding through corners for reinforced structures.
- Profile square, rectangular pipe made of metal, with a rib 20 * 20, 20 * 40, 20 * 60 mm, wall thickness 1.5-2 mm, for large structures 3 mm.
- The aluminum profile is lightweight, easy to install, for construction it is better to use anodized whips, the connections are made with special bolts. Although the cost of the product is high, greenhouses made of aluminum profiles and glass are in demand among gardeners, especially if the sides are made of sliding systems, such a design helps to organize proper ventilation.
- AT recent times the greenhouse from the drywall profile is gaining popularity, the whips are inexpensive, easily cut with scissors for metal, assembled on special fasteners and self-tapping screws. With proper design and compliance with installation standards, the structures are durable, reliable and very practical.
In the photo, a greenhouse made of aluminum profile under glass, when making a project, do not forget to take into account the dimensions of the glass sheet
Advice: In order for a greenhouse made with your own hands from a profile to serve for a long period, it is better to buy galvanized products, the price for them is more expensive than for ordinary metal, but rust is also unlikely if the protective layer is not broken during construction.The use of special connections for fastening metal elements actually allows you to build a collapsible greenhouse frame from a profile with your own hands. Such a structure can be easily dismantled, moved to another place and reassembled.
In the video below, a detailed video on how to make a welded metal greenhouse, from drawing to practical implementation.
Constructive
A do-it-yourself greenhouse built from a profile can be free-standing or made an extension to a house, bathhouse, garage. Independent buildings made of aluminum and a metal profile for drywall are usually rectangular in base, under a gable roof. Wall structures - under a shed. The roof of the house is easy to assemble from a straight profile, no special tools are required. Metal structures made of round and profile pipe often done under an arched roof.
Metal greenhouse under glass with opening roof
How to bend a metal profile for a greenhouse
To bend the profile, you need professional equipment - a pipe bender, the device can be made independently, and in hardware stores there is a service for the manufacture of metal arcs of standard diameter. You can make do-it-yourself arcs for a greenhouse from a drywall profile by cutting the sides with scissors. In the same way, you can make an arch from a professional pipe, cutting it on 2/3 of the width of the profile with a grinder on one side, bend it according to the pattern and weld the seams.
Watch the video instruction on how to make a pipe bender with your own hands, and how to bend a profile for a greenhouse.
Dimensions
The dimensions of a metal profile greenhouse depend only on your ambitions and the size of the site, but when drawing up a drawing, it is important to consider the dimensions of the covering material. The most popular is polycarbonate, its width is 2.0 m, length is 6.0 m, therefore, the vertical and cross sections should be placed so that the edges of the sheets fall into the middle of the profile.
For home use, it is advisable to make greenhouses from a metal profile measuring 6 by 3 m, at least 2.8 m, if the greenhouse is arched, with a radius of 1.9 m, a 6 m polycarbonate sheet is placed exactly along the arc. In addition, metal pipes and profiles can be purchased in lengths of 3 and 6 m, which is very economical, there is practically no waste. With such a width inside, beds of 1.0 m can be arranged, there will be room for a convenient path.
The project of an arched structure for self-construction
The optimal height for an arched metal profile greenhouse is 1.9 m; to increase the height, the structure can be installed on a foundation with a high plinth. In greenhouses with house roofs, it is recommended to make straight walls 1.8-2.1 m high to the lower edge of the slope. From the horizontal along the upper heads to the very high point(ridge) + 0.5-1.2 m more. Given distance regulates the steepness of the slope slope, which depends on the wind and snow loads in the region. For different localities, this figure is 15-45 o.
Shed construction - ideal for an extension to the house
Good to know: The length of the slope can be calculated using the Pythagorean theorem: the square of the hypotenuse is equal to the sum of the squares of the legs, and opposite the angle of 30 ° lies a leg equal to half the hypotenuse.Foundation
For lightweight, temporary greenhouses and hotbeds from a metal profile, the foundation can be omitted, but do not forget that the metal will deteriorate from the ground. Therefore, the site should be leveled, sprinkled with rubble, sand, spread a strip of roofing material around the perimeter, preferably in 2 layers. You can get by with a thick plastic film, but it does not breathe, the base can become damp, rusty.
For full-fledged metal greenhouses, the foundation should be organized in accordance with all standards. It is optimal to make a tape around the perimeter:
- pour monolithic concrete;
- install blocks and fasten them;
- lay out of stone, red brick;
- make 100 * 100 mm from a bar, soaking it with a mixture of mining with bitumen and wrapping it with roofing material;
- use improvised materials: glass bottles, file stumps;
- the base of the channel will also become reliable.
It is better to make the tape not buried, removing only the upper fertile soil by 300-500 mm, or shallow - 700-800 mm. The foundation is being laid according to the scheme:
- crushed stone layer - 100-200 mm;
- sandstone - 100-200 mm, rammed;
- ruberoid is covered;
- a reinforcing frame is installed inside the trench, usually 2 horizontal levels, 2 corrugated rods with a cross section of 8-12 mm each, connected by vertical reinforcement of 6-8 mm can be smooth, the knots are fastened with knitting wire.
- formwork is installed;
- concrete is poured, bayoneted, horizontal is leveled;
- after 2-4 weeks, the shields are removed, vertical waterproofing is done with bitumen, roofing material, backfilling of the soil is carried out.
The height of the tape must necessarily be greater than its width, a high base 100-300 mm above ground level will protect the metal from corrosion
For swampy and very uneven terrain, a pile foundation will be the way out, it is driven or screwed into the ground, usually below the freezing level of the soil. For lightweight greenhouses of their metal profile, a simple option is acceptable: cut 700-1000 mm strips from a 50 * 50 mm steel corner and hammer into the ground, but this solution is not suitable for loose soil.
If the site is damp, it is advisable to install metal greenhouses on columnar foundation. Pits are dug, a pillow is made, pillars are formed from roofing material, reinforcement is installed inside and poured with concrete. You can make poles from metal, asbestos pipes, lay out bricks, stones. For budget, non-buried pillars, a roofing material is placed on the pillow and a regular block, a flat stone, is placed on top; bricks are suitable for small greenhouses.
Foundation from a bar under a metal frame
Do-it-yourself greenhouse from a drywall profile - manufacturing instructions
It is recommended to take a ready-made, standard project for a metal greenhouse, it calculates ergonomics, dimensions, loads. For simple structures, an independent drawing is not difficult. Next, we will offer step-by-step instructions on how to make a greenhouse from an aluminum profile with your own hands, but in this design it is also permissible to use a steel profile.
A drawing of a greenhouse from a profile for drywall, for reinforced structures, it is recommended to install diameters in increments of 50 cm instead of diagonals
Having studied the drawing, it is clear that the entire greenhouse consists of several nodes:
- end with slopes for a roof with a door;
- blind end with slopes under the roof;
- side walls - rectangles consisting of vertical standing and cross-sections for rigidity;
- the ends are pulled together by a long transverse metal profile - a ridge;
- 2 diameters in the middle of the slopes, ribs are installed perpendicularly between them - rafters;
- we sheathe the frame with polycarbonate, a film.
Assembly
According to the proposed algorithm, we collect elements from a metal U-shaped profile for drywall, connect the parts with a crab, as in the photo below.
How to connect a metal profile
We cut the profile to size, according to the drawing, we assemble the ends on a flat area.
Distance between vertical posts is 900-100mm, but not more than 1200mm
We install the end nodes on the foundation, check the geometry, fasten it to the corners and long self-tapping screws. According to the same scheme, we make the sides, the roof, install it in place, make the connection.
How to connect perpendicular parts from a metal profile correctly
We check the metal structure for strength, if necessary, we strengthen it inside with diagonal inserts or add diameters.
The design of the polycarbonate greenhouse on a metal frame is reinforced with additional transverse parts.
It remains to sheathe the metal structure with a covering material. Such a greenhouse made of a galvanized profile with polycarbonate will last more than 10 years, without additional investments. We also offer to see how to make an arched film greenhouse from a metal profile for drywall with your own hands, a step-by-step process in the video.
Greenhouses and greenhouses are a great opportunity to grow the right fruits in risky farming. They differ in designs and materials. Many summer residents prefer greenhouses from a profile pipe, especially since they can be made by hand.
Profile pipes are called pipes, in which the section is not round, but of a different shape, there are oval, square and rectangular. They are very convenient to use in construction. The most popular are pipes with a square and rectangular section, it is from them that the frames of greenhouses and greenhouses are often made. They are made of steel: more often carbon or alloyed, less often stainless.
The profile pipe is similar in shape to a wooden block, but in building structures it is much more profitable - light, durable, protected from corrosion. Greenhouses from a profile pipe, and even made by hand, turn out to be much cheaper than factory ones bought in a store. In addition to economy, they have a number of other advantages.
The rectangular (or square) geometry of the section causes an interesting effect: with a small weight, the professional pipes provide the desired frame strength for greenhouses and greenhouses. Sufficient rigidity of the structure is achieved due to the four ribs of the pipe. Big square the contact of the connecting nodes still adds strength to the entire structure. The details of the greenhouse frame can be connected using welding, self-tapping screws, screws, clamps, the possibility of combining these methods when building a greenhouse with your own hands is also an advantage. Professional pipes are sold with an anti-corrosion coating, which is very convenient: you no longer need to think for yourself how to protect the frame (only the cut points will have to be processed).
The frame of profile pipes has undeniable advantages:
- it is easy to mount and dismantle;
- the design has great strength with low weight;
- parts are universal, easy to load and transport;
- he is not afraid of great physical and mechanical stress.
Light weight can easily turn from an advantage into a disadvantage if the greenhouse is not installed on a solid foundation in areas with strong winds.
Choosing a material
It is easy to make a frame for a greenhouse or a greenhouse with your own hands, if you choose the right material for it. Usually choose between wood, PVC and steel. It is pleasant and quite easy to work with wood with your own hands, it is easy to mount it, it is an environmentally friendly material, but no processing will extend its life. If the greenhouse is made of polycarbonate, then the coating will clearly outlive the wooden frame.
The steel frame is also subject to corrosion, although it is able to withstand heavy loads. Polyvinyl chloride pipes are unlikely to be chosen by a summer resident for making a greenhouse with their own hands because of the high cost, although this material is quite satisfied with its strength, safety and durability.
In search of material, summer residents most often stop at profile pipes, and this is understandable - they make the most reliable greenhouses. They do not rust, withstand heavy loads, do not bend under the snow, and do not require special equipment or experience for installation. It is easy to attach polycarbonate to a steel pipe of rectangular section; thanks to the shape of the section, it is easy to make joints between elements.
Video " Assembling the frame of the greenhouse»
The process of assembling and installing the frame of the greenhouse and the profile pipe. Fastening frame elements.
Drawings and diagram
If the owner of the future greenhouse has decided on the material, then it's time to choose the shape. The choice is not very large.
- An arched greenhouse is usually used for growing low plants. It is convenient because the roof does not need to be cleaned, snow and debris do not linger on it.
- Tall (or climbing high) plants are grown in a tunnel greenhouse. Standard dimensions: width - 10 m, height - 5 m.
- Seedlings are grown in a pyramidal greenhouse, it takes up very little space on the ground, narrow, tending upward.
- The gable shape seems to be the most convenient for those who want to grow plants of a different plan. It makes it possible to rationally manage the space inside the greenhouse, tall plants will be perfectly located in it, and undersized vegetables and berries can be located very compactly in tiers or vertical planting.
- A wall greenhouse is simply half of a gable greenhouse attached to the wall of an existing building.
From a profile pipe it is most convenient to make a gable greenhouse a house - all the elements of the side lie in the same plane. It provides a sufficient amount of light and space for diverse plants, in addition, it allows the installation of additional elements - doors, vents. It is advisable to start the work with the creation of a structure diagram, it will allow you to visualize the owner's ideas about the greenhouse or greenhouse that he is going to build. Moreover, it is the scheme that will help determine the optimal dimensions of the greenhouse so as to make the correct calculation of pipe cutting. And then you need to make a drawing indicating all the dimensions of the greenhouse "house".
The standard length of a profile pipe is 6.05 m. To make one frame out of it, it is necessary to calculate its dimensions according to the diagram. If we assume a height of 1.7 m, then 3.4 m will be needed on two sides, and with a roof angle of 30 degrees, the width will be 2.24 m. The author of the drawing suggests reducing it by 24 cm so that one sheet of polycarbonate is enough for the roof and 10 cm left on the sides for water flow. Since there is a calculation of materials for construction for your money and with your own hands, you should listen to this opinion.
Frame erection
A light greenhouse made of shaped pipes and polycarbonate should be built on a solid foundation. It can be different: wooden, brick, concrete. Most often, a monolithic concrete foundation is made for such a greenhouse, special anchors are laid in it for subsequent fastening of a profile pipe to them. After the concrete has hardened, a profile pipe with a cross section of 40 mm by 20 mm is attached to these anchors, and all frames will be attached to it. Next, you need to assemble the frame, mounting the frames on the base.
most responsible and important point should be the assembly of end frames, on which doors (70 cm wide) and a window vent (80 cm wide) are planned. It is better to make a door from a pipe with a cross section of 40 mm by 20 mm, and for a window, a pipe with a cross section of 20 mm by 20 mm will suffice. Hinges on frames can be installed directly on the assembly site.
Frame frames can be placed at a distance of 1 m from each other - the rigidity and strength of the pipes will allow you to do this without losing the strength of the greenhouse. Moreover, they will be connected by pieces of a square pipe with a cross section of 20 mm by 20 mm, they must be welded flush with the main profile. If the calculation was correct, the polycarbonate will lie flat on the frame. Installation of finished frames begins with an end frame with a door. It must be fixed by welding to the base with two braces from the corner. After 10 cm from the bend, horizontal connections from the pipe are placed, they are needed to fix the polycarbonate.
4407 | 0 |
For self-manufacturing drawings are required from a profile pipe. It is for them that novice greenhouse gardeners build original structures.
The project attracts by the fact that cost and quality are ideally correlated here.
This is the best option for greenhouses / hotbeds in which vegetables and flowers are grown. These products have standard dimensions (multiples of two meters).
Do-it-yourself greenhouses from a profile pipe
A homemade greenhouse is built on the basis of a unique blueprint. Making a pipe will cost the summer resident a mere penny. Before you start building the frame, you should carefully level the area and drive in the pegs so that the profile for the greenhouse from the pipe does not unbend.
To assemble the product, you will need the following materials:
- profile pipes;
- raw materials for hinges;
- tees for pipes;
- film clips;
- wooden or metal pegs;
- corner tees-adapters;
- adhesive mortar and self-tapping screws;
- construction meter.
About square profile greenhouses
Greenhouse gardeners prefer to build structures from shaped pipes for greenhouses, since such a versatile construction material has many interesting properties and characteristics:
- The frame of the greenhouse from the profile pipe is quite durable. It has a thickness of about 1.5 mm and can withstand the load from a large mass of snow.
- If all the details of the frame are coated with a special composition, then the structure acquires good anti-corrosion properties.
- greenhouse arcs can be made stronger by intercepting them with transverse amplifiers.
Modern greenhouses from a profile pipe, built with their own hands, have a variety of shapes. Their construction is very popular when they are on hand from a profile pipe.
The greatest demand is for greenhouses with one- and two-slope roofs, as well as with arched and hip outlines. Depending on the design, greenhouses are divided into:
- Non-separable. Products are used all year round and are not removed for the winter months.
- Collapsible. With the advent of cold weather, greenhouses are dismantled from the pipe and stored in utility room(every meter must be counted).
A greenhouse from a profile pipe consists of the following elements:
- Foundation. This is a rigid and solid part of the structure. It takes on the entire volume of loads, distributing them over the base. Temporary structures do not need strong foundations, but permanent greenhouses cannot do without it. Foundations can be brick, wood, concrete or stone. Structures from a profile pipe will feel great on a monolithic strip foundation. The base of the latter is sealed at a depth of approximately one meter (80 cm below the local freezing point), and then covered with rubble.
- frame. We are talking about the bearing parts of the structure (beams, arcs). They can be made from wood, steel, or polyvinyl chloride (PVC). The stronger the frame, the more stable the greenhouse, made by hand. Each of the varieties has advantages and disadvantages. So, the wooden frame is easy to assemble. However, even if the parts were pre-treated with special water-repellent compounds, the frame assembled from them is still inferior in strength to steel frames. Steel, on the other hand, can withstand heavy loads, but needs anti-corrosion coatings.
- PVC structures. They attract with their safety, strength, flexibility and tightness. However, PVC segments are more expensive than other materials. A self-assembled frame made of profile pipes with a house delights with its reliability. It is supplemented with stiffening ribs (arches). They are located with a two-meter step between adjacent segments. Thanks to the outlines, atmospheric precipitation, which creates loads on the structure, does not linger on the surface of the greenhouse from the pipe. The steel profile of square section does not bend. The frame of such pipes is mounted quite easily. No special equipment is needed here. For the construction of such structures will fit simple circuit greenhouses from a profile pipe.
- Coatings.They are a layer of protective material that is attached to the greenhouse frame. As a result, the harmful effects of the environment cannot affect the plants in the greenhouse. Most often, home-made greenhouses from a profile pipe are covered with film sheets, glass or cellular polycarbonate. They differ in durability, strength or cost. Polycarbonate coating contributes to the creation of the most effective conditions for the development of vegetables: it is impervious to cold air and passes the sun's rays. The polycarbonate coating attracts with its creative aesthetic appearance.
- Accessories.When selecting segments, it is desirable to make a preliminary calculation. Of particular importance is the material going to the coating. So, in order to securely attach cellular polycarbonate, you will need sets of connecting profiles and thermal washers. On a metal base, polycarbonate is fixed with self-tapping screws. With the help of a connecting profile, adjacent polycarbonate sections are combined. Aluminum profiles are supplemented with rubber seals.
Instead of a conclusion
The frame of the greenhouse from a profile pipe allows you to fix various components of the building on the inner plane. It's about complexes. automatic watering, heating or lighting. The galvanized profile is durable because it is not afraid of rust. Among summer residents, greenhouses from a profile pipe made under a film or cellular polycarbonate are very popular. Such structures perfectly keep heat, creating the effect of a thermos inside.
Drawings of greenhouses from a profile pipe
Greenhouse frame from a profile pipe (video)
Let's talk secrets...
Have you ever experienced joint pain? And you know firsthand what it is:
- inability to move comfortably and easily;
- pain during or after exercise;
- discomfort when going up and down stairs;
- inflammation in the joints, swelling;
- unpleasant crunch, clicking not of their own free will;
- causeless and unbearable aching pain in the joints ...
Please answer the question: are you satisfied with this? Can such pain be endured? How much money have you already "leaked" for ineffective treatment? Time to end this! Do you agree? Today we are publishing an exclusive interview with Professor Dikul, in which the doctor revealed the secrets of getting rid of joint pain, treating arthritis and arthrosis.
Did you like the material? Be sure to keep it with you social networks, or just print.
The geometric shape of the section of the hollow profile of a quadrangular shape provides high rigidity of the structure and relative ease of manufacture.
The do-it-yourself scheme of a greenhouse from a profile pipe, shown in the figure below, allows you to evaluate the material consumption and potential labor costs for the construction of the structure. The views and sections shown in the figure are a drawing of fasteners for connecting parts used in the assembly of a greenhouse building.
The designs of greenhouses from a profile pipe of two types are common - with a gable and arched roof shape. standard size greenhouses from a profile pipe is a design with a width of 3 meters and a length of 6 meters.
Making a greenhouse from a profile pipe with your own hands is easier to do with a pitched structure, shown in the diagram above, due to the absence of the need to change the geometry of rolled metal to give it an arcuate profile.
A greenhouse made of a profile pipe with an arc-shaped frame with the same length of structural elements as a pitched building allows you to get a building with large sizes in height and width. The drawing of a greenhouse from a 20x20 profile pipe with an arc profile, presented below, clearly demonstrates this.
Arched greenhouses from a profile pipe have a more ergonomic appearance and greatly simplify the laying of the covering material, whether it be polycarbonate or polyethylene. At the same time, for the possibility of glazing and a longer service life, a greenhouse with a house made of a profile pipe is more suitable.
Important ! The metal profile must be protected from corrosion, otherwise the service life is limited.
How to paint a greenhouse made of metal profile pipes is determined by the state of the surface. With stainless metal - painting is not required, with a surface without traces of rust - a three-layer application of nitro-paint will be sufficient, if the surface is rusty - acid treatment and a multi-layer coating of primer will be required.
double slope design
A do-it-yourself gable greenhouse from a profile pipe is the most common option for manufacturing a structure with a rigid body, designed for long-term operation and suitable for glazing or the use of polymer covering material.
The main component of any greenhouse building is a profiled metal skeleton, which is a supporting structure for fixing a coating that protects crops from atmospheric influences. The frame of the greenhouse building gable roof can be made in two ways:
- Making cuts at three points along the length of the profile, bending at the desired angle and fixing by welding.
- Assembly of segments by connecting individual racks with tees and their mutual fastening with bolted connections.
The drawing of a greenhouse building with dimensions, given below, clearly demonstrates the structural elements that make up its composition and give the necessary rigidity to the finished structure.
The presented greenhouse made of shaped square pipes has a size of 6x4 meters and a gable roof shape, the entrance is offset from the center, which implies beds of different widths. The roof slope is equipped with a window for ventilation and maintaining the required microclimate.
The frame of a greenhouse building is the main load-bearing element and requires careful fastening of structural parts to each other using detachable bolted joints or by welding. For rational use material and minimization of waste (offcuts), the design of a greenhouse building should provide for the use of a solid lash of rolled metal, subject to the width and height of the structure.
The calculation of a greenhouse from a profile pipe in this case is reduced to determining the height of the roof gable [ h], which is an isosceles triangle with a base equal to the width of the building [ S]. The length of the thigh of the triangle in this calculation is determined as half the difference in the length of rolled metal [ L] and twice the height of the side wall of the structure [ H], taking into account the height of the foundation [ h 1 ]. Raising the foundation above ground level reduces the calculated height of the side surface by an amount equal to its double value.
The calculator for calculating the greenhouse structure in this case can be represented by the formula:
The calculation of the frame of the designed structure consists in determining the total length of rolled metal, obtained by summing the length of all parts.
Important ! A 10% length margin is adopted with eight braces, four for each end. With a larger number of stiffeners, an increase in the safety factor will be required.
Frame welding
Welding the frame of a greenhouse structure is necessary to connect the parts to each other and to stiffen the structure.
The scheme of cuts along the length of the lash of rolled metal and its bend, presented below, clearly demonstrate the content of the operations for assembling the main part that makes up the frame of the greenhouse building. Welding is carried out at the bends, allowing you to get a rigid frame element.
arched structure
The manufacture of a greenhouse structure with an arched vault includes the following activities:
- Longitudinal bases with guides for vertical arcs are prepared and attached to the foundation.
- Arcs of the arched vault are being prepared, which will require a galvanized profile pipe for greenhouses with a section of 20x20. The rolled metal is bent 90° around a concrete ring with a diameter of 3 m - this method is a practical solution for obtaining an arc profile, without special devices.
- The vertical arcs are fastened, for which it is inserted and fastened in the guide of the longitudinal base.
- The vertical arcs are connected to each other using longitudinal strips with guides, the size of which is determined by how long the self-made greenhouse from the profile pipe will be.
Below is a diagram of an arched greenhouse building with the designation of structural elements in the manufacture of semi-arcs, and not a single assembly unit in the form of an arch. Such a manufacturing scheme requires a larger number of longitudinal strips, which increases the metal consumption and weight of the structure.
With large dimensions of the arched structure, it will be necessary to connect the parts together by welding. A video of the installation process of a similar design is presented below:
How to bend a profile pipe for a greenhouse yourself
Below is a video demonstrating how to bend a profile pipe for a greenhouse using a homemade pipe bender and answering the question - How to bend a profile pipe for a greenhouse? It is the use of machine tools that makes it possible to achieve a gradual change in the shape of a solid rolled metal and obtain a full-fledged arched vault without the use of additional joints between the elements.
In the absence of a pipe bending machine or fixture, the algorithm for obtaining a bent form of rolled metal can be formulated as follows:
- Bending should be performed around a cylindrical object with a transverse dimension corresponding to the diameter of the arched vault, for example, around a reinforced concrete ring.
- To avoid a sharp bend, fill the inner cavity with sand and seal it at both ends with a wooden plug.
- To avoid displacement, rolled metal should be fixed in a concrete ring in the middle, and to obtain a uniform profile, bend simultaneously in both directions.
- For better bending, the surface of the material can be heated with a blowtorch.
A video demonstrating the operation of a pipe bending machine to obtain a bent form of rolled metal in a garage can be seen below:
Equipment for the manufacture of greenhouses from a profile pipe, in addition to the pipe bending machines discussed above, may include hand tools to obtain a short bend. Also, for processing metal during the manufacturing process, you will need the following power tools: a grinder or an impeller, a welding transformer, a drill with adjustable speed and a screwdriver, if this is not possible.
Ready-made greenhouse from a profile pipe
The greenhouses from the profile pipe shown in the photo below clearly demonstrate what can be achieved if you want to build a greenhouse building on a personal plot with your own hands.
Friends, prefabricated structures are widely used not only in industrial construction, but also in agriculture. So metal greenhouses made of polycarbonate with a light profile frame are affordable and very convenient to assemble and transport. In this article, you will learn what such a structure as a “metal greenhouse” is, the frame assembly process and the main components of the device.
Overview of the greenhouse device
Metal greenhouses are good because they can be assembled and disassembled on their own, with their own hands using improvised tools. When installing the greenhouse structure for a long time without moving to another place, it is recommended to prepare the base more responsibly, perhaps even a small foundation. If the greenhouse will move from place to place, then there is no need to spend much effort on the mounting surface, since the weight of the structure is light, and due to the design, it is possible to achieve a good stability result at any time of the year under any weather conditions.
Do-it-yourself greenhouse frame assembly
To assemble the structure ourselves, we need square metal pipes.
Frame parts set:
- pipes six-meter square section size 40x20 in the amount of 9 pieces
- pipes 97 cm square section size 40x20 in the amount of 60 pieces
- pipes 2.5 meters long square section size 40x20 in the amount of 6 pieces
- pipes with a length of 2.3 meters of square section with a size of 40x20 in the amount of 4 pieces
- as well as 4 pcs. pipes 1.2 meters each and one pipe 0.9 meters long with a section of the same size (40x20).
Attention: these data are given as an example as one of the typical projects for construction, we recommend that you perform the correct calculation, since metal carcass for a greenhouse can have both standard and individual dimensions and characteristics, depending on the requirements for the place and the weather conditions of the environment.
Assembly process
Polycarbonate metal greenhouses have proven themselves very well in various regions of Russia, thanks to their stability and endurance in bad windy weather.
Before beginning installation, make sure the surface is clear of medium to large debris and is nearly perfectly level. The horizontal of the installation is very important so that the metal frame of the greenhouse does not warp. The installation process begins with welding 7 pipes 6 m long to each other, having previously processed them with a steel bending machine, which changes its shape into a semicircle. A steel bender, or as it is also called a “sheet bender”, is an interesting device that can be found in any city where there is a metal-rolling base.
For sheathing, we need polycarbonate with a sheet width of 2.1 meters. On the basis (surface) we put two six-meter pipes and two across, visually it will resemble the shape of a rectangle.
Method of installation of the structure
First of all, you need to check the geometry of the diagonals (the accuracy of the angles), which should fit snugly against each other and be symmetrical with a maximum deviation of 2-3 millimeters.
The second step in the installation of the greenhouse will be welding the arcs with a step equal to half the width of the polycarbonate sheet, that is, if the width of the standard sheet is 2.1 meters, then the arcs must be welded from the beginning of the frame after 1 meter 5 centimeters. This calculation can be taken for the construction of any arched greenhouse, 1:2 width = arc installation step.
After the installation of semicircular pipes, it is necessary to check the vertical geometry of the extreme elements. This is done with a special plumb line or, as the common people call it, a “weight”. The weight is attached to the top point of the arc and must match the jumpers below. If there is no match, then the arc is littered and needs to be aligned.
If the arcs are already installed, you can carry out the transverse crate of the greenhouse. This is done as follows: lightly weld the transverse steel pipes in increments of 0.6 meters.
Checking the diagonals
An important stage in the construction of a metal greenhouse made of polycarbonate. If the dimensions of the diagonals are inaccurate and the error is more than 3-5 millimeters, it will be necessary to check the entire set of the structure frame for accuracy.
Remember that polycarbonate metal greenhouses are easy to install, but you need to be extremely careful when installing the frame, since the accuracy of the installation depends on the further correctness and accuracy of the work on the arrangement and roof sheathing, and if the structure initially diverges even by some 1-2 centimeters , then discrepancies in sheathing cannot be avoided.
First of all, carefully inspect the extreme arcs, if they are filled up, then the sheer load will be slightly deflected to the side. In this case, you need to bend the arc in the opposite direction. You need to check it accurately, according to successful results, you can weld the frame with an arc.
Important information: the frame of the greenhouse made of thin-walled profile is subject to deformation of individual structural elements, so the work on fixing the frame (welding or screwing with self-tapping screws) must be carried out after the arcs are fixed vertically properly.
Polycarbonate greenhouse ends
The next step is to install a doorway, for which we need square pipes of 40mm in size: 2.3 and 2.5 meters.
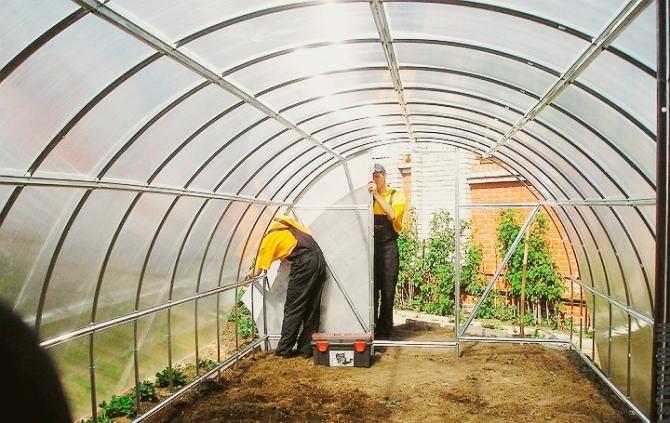
The last step in the construction of a metal greenhouse in the first way will be the anti-corrosion treatment of the frame, priming and painting the metal structure as desired.
Video:
div > .uk-panel")" data-uk-grid-margin="">