With a competent approach, the insulation of the balcony and its decoration can be done economically, but at the same time with high quality. For example, finishing a loggia with plastic panels opens up wide possibilities for design in different colors and looks stylish and aesthetically pleasing. And every owner of an apartment can afford this type of sheathing! After all, it will cost less than MDF paneling, not to mention natural wood or other materials.
The company "Eurobalcon - 24" has been providing services to residents of Moscow and the Moscow region for many years in sheathing, glazing and insulation of loggias and balcony structures. Balcony decoration PVC panels produced by our craftsmen at a high professional level and at very affordable prices!
What is the advantage of plastic panels for the balcony
PVC panels for the balcony are made from rigid polyvinyl chloride. They are suture, seamless and glossy. To increase the strength, stiffeners are provided on them, and for protection they are coated with a polymer film. Light planks of various lengths and widths perfectly combine aesthetic appearance and practicality of use.
Plastic panels for a balcony have a number of important advantages that allow them to successfully compete with other materials:
- Can be used on any surface;
- Resistance to moisture, temperature extremes;
- The material does not support combustion;
- Improvement of heat and sound insulation;
- Simplicity and high speed of installation;
- Wide color range of products;
- Attractive appearance;
- Unpretentiousness in care;
- Low cost;
- Durability.
Sheathing the balcony with plastic panels goes well with PVC window structures and any kind of insulation. It hides all the flaws on the walls, does not emit toxic substances, does not fade in the sun, does not require special care. Even stubborn dirt can be easily removed with conventional detergents. The service life of such a finish is at least 10 years.
A wide selection of the most modern finishing materials makes it possible for each consumer to purchase the best option for himself in all respects. This must be done consciously, clearly presenting the advantages and disadvantages of each of them. In this article, we will talk about only one material - PVC plastic panels for balconies.
In areas with an unfavorable climate, the importance of balconies cladding with simultaneous insulation increases significantly, and the requirements for the quality of panels also increase. Depending on the wishes and architectural features of the building, balconies can be upholstered only from the outside, only from the inside, or from both sides. At the same time, glazing is installed on the balconies first. A balcony converted in this way can easily be attached to living quarters, thereby increasing the useful area of \u200b\u200bthe kitchen, hall or bedroom, depending on which room it adjoins.
- Internal lining. All construction work is carried out from the inside, external surfaces remain intact. Not a very popular method, the appearance of such a design leaves much to be desired. It is used only in cases where insulation is not done.
- Outer skin. This method can be found more often, but among young developers this option is not considered acceptable. It is also used only when arranging a cold balcony. If with outside the balcony is ennobled, then from the inside its view satisfies few people.
- Complex upholstery. Materials are fixed both from the outside and from the inside of the structure. The most popular method at present allows you to create warm rooms, significantly improves the microclimate on the balcony. It is possible to make a warm floor on it, install furniture, eliminate the wall between it and the adjacent living space.
Plastic panels for the balcony are produced by numerous companies, there is still no single common standard. Each is guided by its own specifications, best suited to the capabilities of the available equipment. Most often, the length is 2.7 meters, the thickness is 10 mm, but these dimensions can vary widely. The color, texture of the front layer, the type of castle, etc., for the most part, are not regulated.
First of all, you need to pay attention to the maximum and minimum operating temperatures, resistance to hard ultraviolet radiation, thickness and type of castle. These are the physical characteristics of the materials. As for design indicators, there is no universal recommendation here. Professionals advise to take into account the interior of the premises and the appearance of the facade of the building. Select material in such a way that it fits organically into existing design solutions. By color solutions the product range includes more than 180 types.
What to look for when choosing?
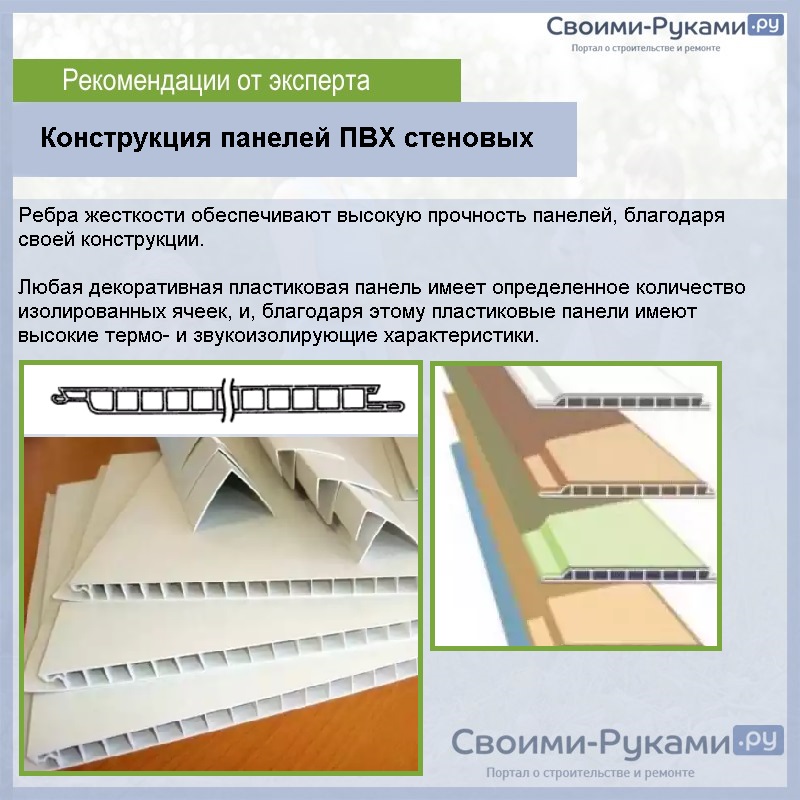
Advantages and disadvantages of PVC panels
If the manufacturer is conscientious, the material is of high quality, the equipment is modern, and the manufacturing technology is not violated, then PVC panels have much more advantages than disadvantages.
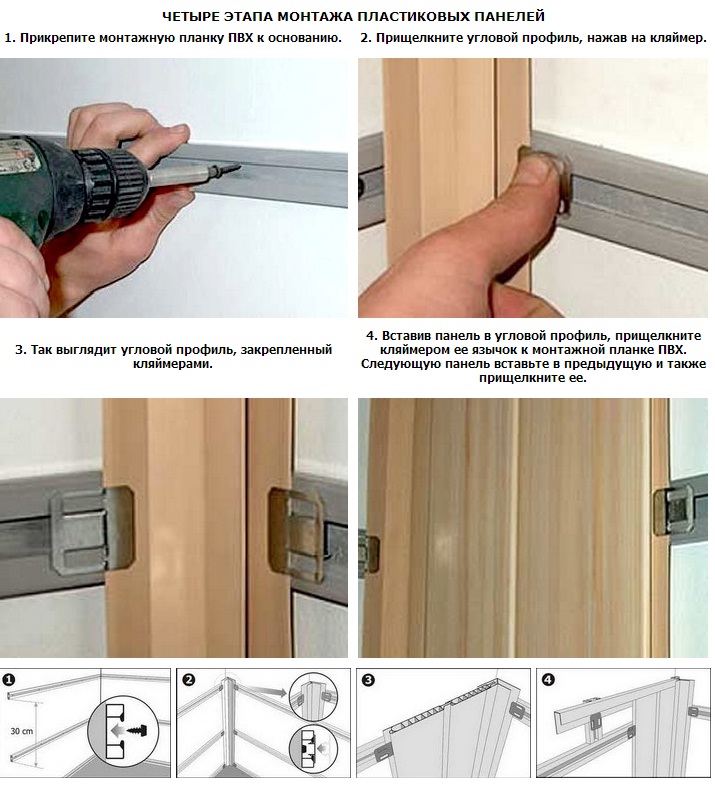
Weaknesses: insufficient physical strength, flammability, in terms of safety it is difficult to attribute to completely environmentally friendly materials.
The technology of cladding balconies with PVC panels
The dimensions, material of manufacture and the appearance of the texture should be selected depending on the place of use, interior design and financial capabilities. After a decision has been made on the types of panels and the method of finishing, you can proceed to the direct execution of work.
Step 1. Checking the condition of the parapet and the bearing reinforced concrete slab.
Most of the old balconies have metal parapets; over the years of operation, the bearing indicators of metal structures have lost their original characteristics. They need to be removed completely or overhauled. The best option is to put a foam block fence instead of a metal parapet.
But the decision should be made on the spot by a professional master after evaluating many factors and taking into account the wishes of the owners. We recommend installing foam blocks if possible, they have low thermal conductivity, but strength is sufficient to withstand the installation of glazing. In addition, it is very easy to attach PVC panels to them for finishing.
Step 2 Counting the number required material, measurement of surfaces, selection of the method of fastening panels.
What are the methods of fixing the panels?
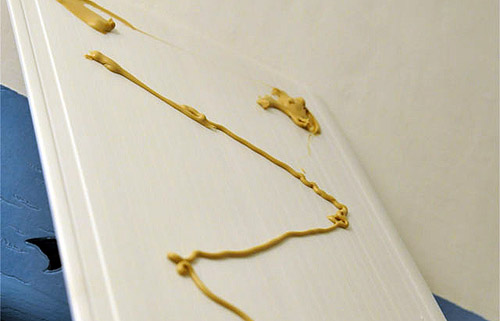
Depending on the chosen method of fixation, purchase materials and additional elements. As an example, a lightweight option for finishing a balcony with PVC panels will be considered - along the parapet.
Step 3 Preparation of the metal frame. To do this, metal strips are welded to the parapet at certain distances, the strips are about 10 cm long, 2–3 cm wide, and ≈ 2–3 mm thick. The strips are installed on both sides of the parapet, while taking into account the thickness of the insulation. For most cases, a thickness of 10 cm is sufficient, this will have a positive effect on heat saving and not reduce usable area balcony.
Step 4 Holes Ø 5–6 mm must be drilled in metal strips to fix the rails. The rails are fastened with bolts, the nut must be tightened until the bolt head is completely sunk into the tree. If there is a desire, then a large diameter hole can be drilled under the head, the depth of the hole is equal to the thickness of the head.
Important. The slats must first be installed on the outside of the parapet, then a plastic film for waterproofing should be attached with a stapler, insulation should be installed, and only after that the slats should be installed from the inside.
As a heater, it is better to take foam plates of the appropriate thickness. They have high rates of heat saving, at the cost of the most affordable. And the amount of chemical compounds released into the air is not of great importance for balconies.
Step 5 Cut PVC panels to size, prepare end and corner strips. These additional elements must be purchased at the same time as the panels. Keep in mind that during cutting, the dimensions should only go minus (no more than 0.5 cm), but not plus.
If there is a desire or this is required by the technology for mounting large PVC panels, then instead of rails to metal strips, moisture-resistant plywood or OSB boards should be fixed. In the future, the fastening of the finishing skin is carried out using liquid glue.
Step 6. Work should start from one of the corners of the balcony and then move in a circle. Very carefully fix the first panel, carefully check its position with a level. If there is not enough experience, then it is recommended to check the correct spatial position of the plates after two or three rows.
PVC panels - trim strips (moldings)
Practical advice. If it is found that the plate is not in a vertical position, then the error should be corrected gradually. Move each next plate no more than one millimeter, otherwise the marriage will become noticeable. The casing is fixed with a stapler, the length of the staples is not more than 6 mm.
Carefully finish the installation sites of windows and doors, remember that the ends of the sheathing must necessarily have a stop, and not hang freely in the air.
PVC panels can be fixed with a stapler
Step 7 In the same way, sheathe the outer surfaces of the parapet. Pay attention to the tightness of the individual panels in the locks, do not allow gaps. For sheathing external surfaces, you need to purchase only materials that are resistant to UV rays. If you do not adhere to this rule, then after 2–3 years the outer skin will lose its plasticity and will crack at the slightest load.
Step 8 The ceiling is finished according to the same algorithm, if desired, insulation can be made.
Video - Types of plastic panels
When planning a balcony renovation, many are faced with the difficult problem of choosing decorative finishing materials. At the initial stage, the question is usually formulated as follows: "Wood or plastic?". Wood, of course, is natural and environmentally friendly, but nevertheless, plastic panels for a balcony remain the most popular material. And they are presented on the market in such a huge range that it is very difficult for an inexperienced buyer to make a choice.
Let's try to figure out what plastic panels for finishing a balcony are in general, how they differ from each other and what advantages and disadvantages they have.
What is good and bad plastic
First of all, we note that the popularity of plastic did not appear from scratch. So, plastic panels for the balcony:
- durable (warranty period - 10-30 years);
- durable, resistant to mechanical stress due to stiffening ribs;
- moisture resistant;
- do not emit any toxic and harmful substances;
- not afraid of frost, do not fade in the sun;
- do not support combustion, fireproof;
- easy to install (even a beginner can handle it);
- antistatic, do not attract dust and dirt;
- do not require special care (wash with plain water or wipe with a damp cloth);
- have many color shades and imitations for natural materials;
- cheap.
There are only two significant drawbacks to plastic panels, and it is they who sometimes scare away buyers. This is the unnaturalness of the material and the specific smell of plastic, which is sometimes felt after installing the panels.
For residential premises, this, of course, can be a serious argument against the use of plastic. But when finishing a balcony, these shortcomings do not matter. The smell will disappear without a trace in a few days, and natural wooden lining, after being treated with all kinds of impregnations and varnishes, will differ little in terms of environmental friendliness from harmless plastic.
Besides , PVC panels for the balcony, although durable, but up to brick wall they are far away. Strong impacts and sharp objects can damage them. And if you come across low-quality plastic, then with sudden temperature changes it can be deformed.
Types of plastic panels
Balcony panels differ in four positions: size, manufacturing method, method of connecting panels to each other and type of coating. Let's see what they are.
The size
There are three types of balcony plastic:
Wall panels
- wall (sheet) panels and plates. Width - from 25 cm to 2.44 m, length - from 2.5 to 6 m. Used for sheathing any horizontal and vertical surfaces. For decorative finishes balconies and loggias are most often used planks 25-40 cm wide;
- lining. Type-setting rails 10-20 cm wide and up to 6 m long. They are used both for balcony walls and for ceilings. They are connected to each other according to the "protrusion-groove" principle. To make the walls appear higher, the lining is mounted vertically;
- tile. Square shape with a side of 30 cm to 1 m. It is mainly used for the ceiling, but some also use it for walls. It turns out unusual and original design, especially if you arrange the tiles in a checkerboard pattern or build a mosaic.
Connection method
According to the method of docking, PVC balcony panels are suture and seamless. Each method is good in its own way. Plastic lining for a balcony makes the wall embossed and gives seams that visually lengthen the room. When using wall panels for a balcony, a beautiful, even, seamless surface is obtained.
Preparation method
Wall panels for finishing the balcony are made either by the usual pressing and stamping method, or in the form of sandwich panels.
Ordinary Wall panels on the balcony are made from polyvinyl chloride (PVC) - a synthetic polymer consisting of 57% rock salt and 43% petroleum products, including various stabilizing and strengthening additives, as well as pigment dyes. The finished product is light, high-quality, environmentally friendly, durable, beautiful and cheap.
Balcony sandwich panels are a new modern finishing material consisting of two PVC sheets, between which a heater is laid (usually expanded polystyrene or mineral wool). Sandwich panels are double-sided, that is, with two front sides, and one-sided.
Sandwich panels
Bilateral panels are usually used for mounting all kinds of partitions, and one-sided - for walls and slopes. Their front side is made of more durable plastic which gives the panel extra strength. The usual thickness of the "sandwich" is 10, 24 and 32 mm.
The main advantage of sandwich panels is that they do not need additional vapor and waterproofing. In addition, they have the main positive properties of plastic (moisture resistance, light resistance, durability, etc.). A balcony made of sandwich panels will be seamless, cozy, and most importantly - warm.
In addition to the high cost, sandwich panels have only one drawback: due to the large size of the sheet (1.5x3 m), you will have to tinker with their installation. You need to carefully make calculations in order to cut off the desired piece and not make a mistake. Such panels are attached to nails, screws or special glue.
Coating type
The coating of plastic panels also varies. So, in the market of building materials you can find three types:
Laminated panels
- laminated panels. A special PVC film is glued to the surface of the plastic. It can be either plain color or textured - wood, metal, leather, marble, bamboo, etc. Laminated PVC panels for the balcony are antistatic, less dirty, durable enough. And thanks to the successful combination of price and quality, they are the most popular;
thermal printed panels
- PVC panels with thermal printing. The drawing is transferred to plastic using a special thermal film. This method allows you to make any pattern on the panels, even a photograph of the customer. In this case, all colors are brighter and more saturated. A lacquer coating is applied on top, which provides additional protection for the pattern from chemical and mechanical damage, and at the same time gives it shine;
Offset printed panels
- offset printed plastic panels. The desired pattern is printed on the panels with a typographic form, after which it is varnished. Images can be very diverse, but the most common ones look like natural stone (marble, onyx, basalt, malachite, etc.).
As you can see, you can choose the material for every taste and color. The main thing is to decide on the design.
Good luck with your repair!
A wide selection of the most modern finishing materials makes it possible for each consumer to purchase the best option for himself in all respects. This must be done consciously, clearly presenting the advantages and disadvantages of each of them. In this article, we will talk about only one material - PVC plastic panels for balconies.
In areas with an unfavorable climate, the importance of balconies cladding with simultaneous insulation increases significantly, and the requirements for the quality of panels also increase. Depending on the wishes and architectural features of the building, balconies can be upholstered only from the outside, only from the inside, or from both sides. At the same time, glazing is installed on the balconies first. A balcony converted in this way can easily be attached to living quarters, thereby increasing the useful area of \u200b\u200bthe kitchen, hall or bedroom, depending on which room it adjoins.
- Internal lining. All construction work is carried out from the inside, external surfaces remain intact. Not a very popular method, the appearance of such a design leaves much to be desired. It is used only in cases where insulation is not done.
- External cladding. This method can be found more often, but among young developers this option is not considered acceptable. It is also used only when arranging a cold balcony. If from the outside the balcony is ennobled, then from the inside, few people are satisfied with its appearance.
- Complex upholstery. Materials are fixed both from the outside and from the inside of the structure. The most popular method at present allows you to create warm rooms, significantly improves the microclimate on the balcony. It is possible to make a warm floor on it, install furniture, eliminate the wall between it and the adjacent living space.
Plastic panels for the balcony are produced by numerous companies, there is still no single common standard. Each is guided by its own specifications, best suited to the capabilities of the available equipment. Most often, the length is 2.7 meters, the thickness is 10 mm, but these dimensions can vary widely. The color, texture of the front layer, the type of castle, etc., for the most part, are not regulated.
How to choose PVC panels
First of all, you need to pay attention to the maximum and minimum operating temperatures, resistance to hard ultraviolet radiation, thickness and type of lock. These are the physical characteristics of the materials. As for design indicators, there is no universal recommendation here. Professionals advise to take into account the interior of the premises and the appearance of the facade of the building. Select material in such a way that it organically fits into existing design solutions. In terms of color solutions, the product range includes more than 180 types.
What to look for when choosing?
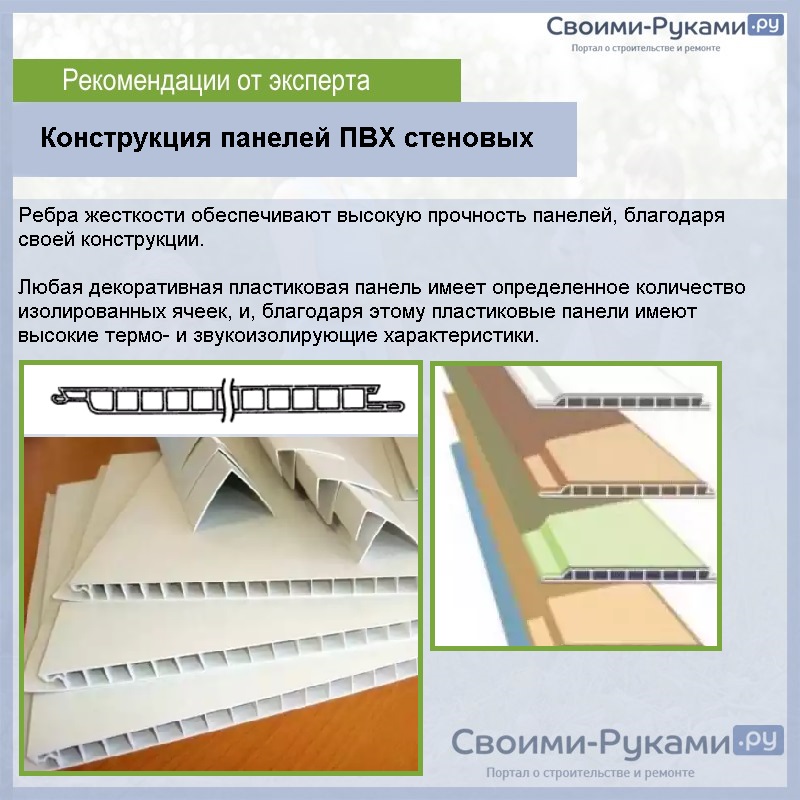
Advantages and disadvantages of PVC panels
If the manufacturer is conscientious, the material is of high quality, the equipment is modern, and the manufacturing technology is not violated, then PVC panels have much more advantages than disadvantages.
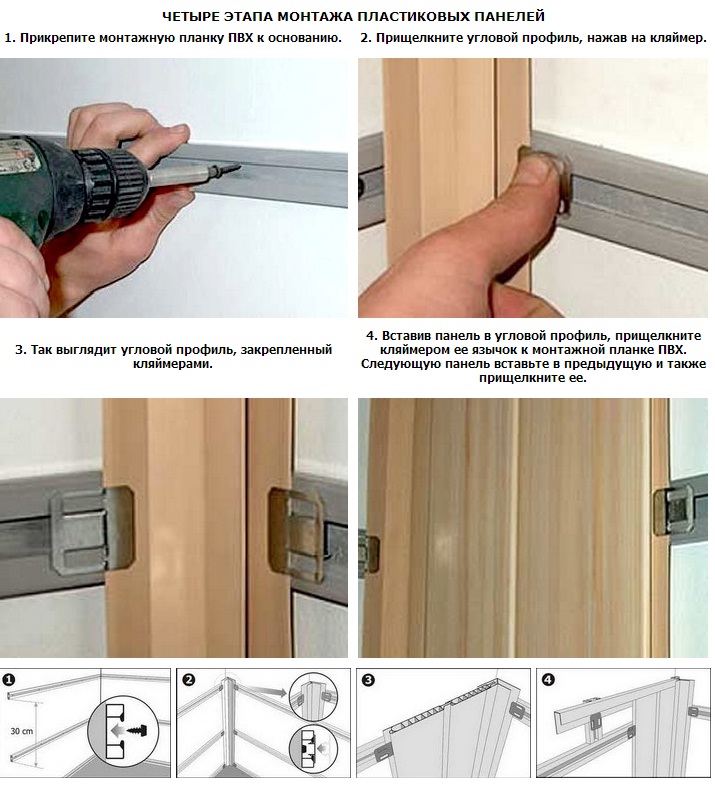
Weaknesses: insufficient physical strength, flammability, in terms of safety it is difficult to attribute to completely environmentally friendly materials.
The technology of cladding balconies with PVC panels
The dimensions, material of manufacture and the appearance of the texture should be selected depending on the place of use, interior design and financial capabilities. After a decision has been made on the types of panels and the method of finishing, you can proceed to the direct execution of work.
Step 1. Checking the condition of the parapet and the supporting reinforced concrete slab.
Most of the old balconies have metal parapets; over the years of operation, the bearing indicators of metal structures have lost their original characteristics. They need to be removed completely or overhauled. The best option is to put a foam block fence instead of a metal parapet.
But the decision should be made on the spot by a professional master after evaluating many factors and taking into account the wishes of the owners. We recommend installing foam blocks if possible, they have low thermal conductivity, but strength is sufficient to withstand the installation of glazing. In addition, it is very easy to attach PVC panels to them for finishing.
Step 2. Calculating the amount of material needed, measuring surfaces, choosing a method for attaching panels.
What are the methods of fixing the panels?
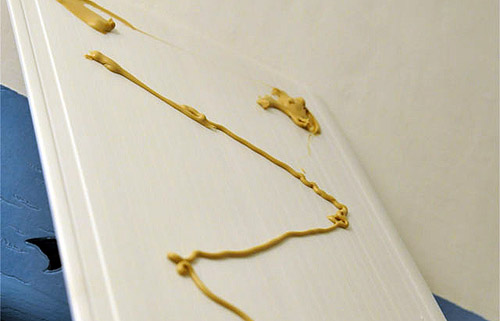
Depending on the chosen method of fixation, purchase materials and additional elements. As an example, a lightweight option for finishing a balcony with PVC panels will be considered - along the parapet.
Step 3. Preparing the metal frame. To do this, metal strips are welded to the parapet at certain distances, the length of the strips is about 10 cm, the width is 2–3 cm, the thickness is? 2–3 mm. The strips are installed on both sides of the parapet, while taking into account the thickness of the insulation. For most cases, a thickness of 10 cm is sufficient, this will allow you to have a positive effect on heat saving and not reduce the useful area of \u200b\u200bthe balcony.
Step 4. Holes Ø 5–6 mm must be drilled in metal strips to fix the rails. The rails are fastened with bolts, the nut must be tightened until the bolt head is completely sunk into the tree. If there is a desire, then a large diameter hole can be drilled under the head, the depth of the hole is equal to the thickness of the head.
Important. The slats must first be installed on the outside of the parapet, then a plastic film for waterproofing should be attached with a stapler, insulation should be installed, and only after that the slats should be installed from the inside.
As a heater, it is better to take foam plates of the appropriate thickness. They have high rates of heat saving, at the cost of the most affordable. And the amount of chemical compounds released into the air is not of great importance for balconies.
Step 5. Cut PVC panels to size, prepare end and corner strips. These additional elements must be purchased at the same time as the panels. Keep in mind that during cutting, the dimensions should only go minus (no more than 0.5 cm), but not plus.
If there is a desire or this is required by the technology for mounting large PVC panels, then instead of rails to metal strips, moisture-resistant plywood or OSB boards should be fixed. In the future, the fastening of the finishing skin is carried out using liquid glue.
Step 6. Work should start from one of the corners of the balcony and then move in a circle. Very carefully fix the first panel, carefully check its position with a level. If there is not enough experience, then it is recommended to check the correct spatial position of the plates after two or three rows.
Practical advice. If it is found that the plate is not in a vertical position, then the error should be corrected gradually. Move each next plate no more than one millimeter, otherwise the marriage will become noticeable. The casing is fixed with a stapler, the length of the staples is not more than 6 mm.
Carefully finish the installation sites of windows and doors, remember that the ends of the sheathing must necessarily have a stop, and not hang freely in the air.
Push the panel firmly into the corner profile
Step 7. In the same way, sheathe the outer surfaces of the parapet. Pay attention to the tightness of the individual panels in the locks, do not allow gaps. For sheathing external surfaces, you need to purchase only materials that are resistant to UV rays. If you do not adhere to this rule, then after 2–3 years the outer skin will lose its plasticity and will crack at the slightest load.
Step 8. The ceiling is finished according to the same algorithm, if desired, insulation can be made.
Connecting power to lights
If you plan to use the balcony as part of the room, then it is advisable to install additional lamps. Wiring must be pre-laid on the ceiling or wall under the sheathing. It is recommended to use modern economical lamps. Practitioners are advised to install at least one outlet on the balcony. If it is not currently needed, then no one can guarantee that it will not be needed in the future. For wiring, it is better to use the services of a professional electrician. Cables will have to be connected to junction boxes, and it is very difficult for an amateur to find them.
Video - Types of plastic panels
First you need to decide on the type of skin. And this is not easy to do, because a large assortment of materials is simply amazing! If you want to make the room neat and beautiful, while keeping within a modest budget, then the choice narrows somewhat.
In the end, many stop at the balcony sheathing with PVC panels. Why is this finish so popular? What are its features, pros and cons? Let's try to answer these questions in today's article. But first, let's figure out which panels for the balcony are most suitable. To do this, get acquainted with their range.
Finishing with plastic panels is quite popular lately.
Classification of PVC panels
Plastic panels are three-dimensional polyvinyl chloride strips, inside of which there are longitudinal stiffening ribs. It is possible to sheathe a balcony with seamless plastic panels, which form an integral canvas when assembled, and with seam ones, which, when connected, form a gap between the elements. In the latter case vertical stripes seams will visually "pull" the room up. Panels differ on such grounds.
The size
Standard panels have a length of 2.5 to 6 m and a width ranging from 44 to 244 cm. From this range, PVC panels with a width of 25 to 40 cm are used for finishing the loggia. Plastic lining has a narrower width of the board (10-20 cm) . It is also used for finishing the ceiling.
Coating type
Wall cladding materials vary in surface finish. This can be thermal printing, during which the pattern is transferred to the material with a special thermal film. The method is good because it allows you to apply bright saturated images of any degree of complexity, including photographs. The film is covered with a layer of varnish that protects it and gives the surface an attractive sheen.
Good to know!
Another option for drawing a picture on a panel - offset printing - involves displaying a picture on a panel using a printing form and then opening it with varnish.
The image can be anything (even a photograph). In practice, the most popular is imitation natural stone: onyx, marble, malachite or basalt.
The third finishing option is fundamentally different from the previous two. It involves gluing a laminated film onto the plastic surface, which can have a different pattern and texture, repeating natural materials (wood, stone, bamboo, leather, etc.). Such material is easy to care for, antistatic and inexpensive. This explains the popularity and demand for plastic panels for finishing the balcony.
The choice of colors of plastic panels is very wide.
Preparation method
PVC panels are produced in two versions: pressing and stamping products and sandwich panels. Both methods have their advantages and disadvantages. Let's consider them.
- Standard plastic for surface cladding is produced by pressing polyvinyl chloride - a polymeric material that includes 43% petroleum products, stabilizing components and pigments, as well as 57% rock salt.
- Sandwich panels are a new word in the industrial production of plastic. Them spatial form implies the presence of 2 layers of PVC with insulation in the form mineral wool or styrofoam in the middle. One-sided "sandwich" has a stronger front side and is used for sheathing slopes and walls. The bilateral form is used for production of partitions. Both versions are available in 10, 24 or 32 mm thicknesses.
Due to their composition, sandwich panels do not need additional insulation, hydro and vapor barrier. Some inconvenience at work creates them big sizes 1.5 * 3 m and the need to cut out parts of the desired shape.
Pros and cons of cladding a balcony with plastic
Plastic has become ubiquitous in our everyday life. He is everywhere. And it is not surprising that it is also used for cladding balconies. What are the advantages of this versatile material?
Pros:
- environmental friendliness due to the absence of toxic substances in the composition of polyvinyl chloride;
- moisture resistance;
- ease of installation: plastic is easily installed on any type of surface and does not need to be pre-leveled;
- simple maintenance, consisting in wiping the surface with a damp cloth;
- light weight, which is of particular importance: plastic panels for the balcony should not overload the structure;
- low price;
- a rich color palette and a variety of textures that can satisfy the needs of the most demanding consumer.
However, plastic is not perfect. Like any material, it has certain disadvantages. Compared to the advantages, they are insignificant, but it is impossible not to mention them.
Minuses:
- the ability to exude an unpleasant odor when strongly heated or ignited;
- susceptibility to jumps temperature: panels can be deformed from frost, so their use is advisable only on a warmed loggia or balcony;
- resistance to mechanical damage. Especially with regard to cheap thin types of PVC; therefore, it is recommended to finish the balcony with plastic, the thickness of which is at least 8 mm.
Advantages of plastic panels - ease of installation and beautiful appearance
Types of mounting profiles
Sheathing a balcony with plastic panels involves the use of several types of special profiles. So, a straight mounting profile is attached to the crate from the side of the cross member or through the wide side part. Corner dihedral profile is installed on the outer and inner corners.
Step-by-step instructions for self-finishing
Sheathing a balcony with plastic panels with your own hands is not particularly difficult. It can also be performed by a beginner in repair who does not have special skills. The main thing in this matter is perseverance, scrupulousness, strict adherence to the instructions below. And the availability of the necessary tools that should be prepared in advance so as not to run after them to the store at the most inopportune moment. So, for work we need:
- screwdriver equipped with a magnetic nozzle;
- perforator or drill;
- mounting foam;
- building level;
- plastic corners;
- plinth;
- window profiles;
- insulation (polystyrene foam or mineral wool);
- suspensions;
- profiles made of galvanized metal;
- small dowels or screws.
crate
An important stage that is performed after performing steam, waterproofing and insulation before sheathing the balcony with plastic. On the crate, as on the frame, the entire sheathing subsequently rests. Therefore, its installation should be given Special attention. It is produced in this order. The location of the frame is outlined. Then a profile with a U-shaped section is attached to the wall with an interval of 50-70 cm on dowels or self-tapping screws.
Some stages of installation of plastic panels
Ceiling plastic sheathing
Finishing the loggia starts from the ceiling. After installing the metal frame, work is carried out in the following sequence.
- Fasten around the ceiling starting profiles from galvanized metal.
- Punch holes in the profile and the wall with a puncher, insert dowel-nails there and screw the structure to the wall using a screwdriver with a magnetic nozzle.
- Attach a galvanized profile to iron hangers in the middle of the ceiling. With a loggia width of 1.2 m, one central profile is sufficient. If the room is wider, then two will be needed.
- Attach the starting profiles under the plastic panels to the central profile.
- Stretch the wiring to future fixtures (most often these are built-in point light sources).
- Paste First plastic panel into the starting profiles, fasten with self-tapping screws to the guide profile and along the edges.
- Install subsequent panels end-to-end to the previous ones, similarly screw them to the metal profile with self-tapping screws.
- Trim the last panel to the desired size so that it extends 5 mm beyond the previous panel, and not 7, as usual. Swap the penultimate and last panels in places and push the last panel so that it enters the outermost profile without a visible gap. If necessary, use plastic moldings to adjust the length of the trim elements.
wall decoration
After finishing the ceiling, they begin to sheathe the walls with plastic, starting from the space under the window. In this case, the actions are largely similar to the previous work.
Wall cladding with plastic panels
- Attach the metal profile to the window sill from below. Check the location of the side profiles on it using the building level.
- Fix the profile to the floor level.
- In the middle of the wall. Located under the window, install several metal hangers at a distance of about 50 cm from each other.
- The void between the wall and metal frame fill with insulation, and seal the cracks with mounting foam.
- Fasten the guide metal profile to the hangers.
- Install PVC panels on the installed profiles using dowel-nails or self-tapping screws.
- Close the gaps between the floor and the plastic wall cladding with skirting boards. install a special ceiling plinth at the joints between the ceiling and walls.
Finishing the balcony with PVC panels is finished. As you can see, there is nothing complicated in it. Plastic belongs to a rare category of materials that combine low cost and attractive appearance. Thanks to plastic cladding, you can inexpensively and quickly ennoble any balcony or loggia.